Breadcrumb
The Connected Future of Manufacturing
Akira Yamashita, the new divisional head of Panasonic Factory Solutions in Europe, believes the future of manufacturing is a connected world, where connected equipment works in harmony with connected operators. He explains his vision…
Much has been spoken about the autonomous future of manufacturing. Although many of the processes that have been manual in the past will continue to be automated, I see the future of smart factory production as a much more connected world. One where connected equipment works in harmony with fewer but more connected human operators using IoT solutions to manage real-time performance and to provide real-time process transparency.
With more than 100 years of experience manufacturing a wide range of electrical and electronic products on an international scale, Panasonic is in a unique position to make this connected smart factory environment a reality. We continue to take our daily experience of production in our own manufacturing facilities and use it to develop our own Smart Factory Solutions for our customers.
Rapid adaptation is required
With the macro-economic and geopolitical environment highly volatile and consumer habits rapidly changing, it is placing huge pressures on supply chains. As a result, manufacturers are having to react rapidly and require assembly lines that can be adapted quickly to these changing needs.
Our purpose is to help these companies to further automate their factories and to reduce total cost of ownership using 5M management – the management of Man, Machine, Material, Method and Measurement - to improve overall equipment effectiveness with 5M process control.
At the heart of these solutions is the use of connected edge technologies, such as sensors, to deliver AI-based autonomous control of individual equipment, the assembly line and wider production environment.
In the SMT area, we offer turnkey solutions for manufacturing challenges from our portfolio of hardware such as screen printing, SMT/THT/PTH equipment, odd form component placement as well as FATP solutions. In addition, we provide MES software for overall optimisation, flexible modular solutions for production planning and analysis, design and simulation, asset management, material management, product changeover and traceability.
An example of this progress in action is the Panasonic APC-5M assembly line system concept, which identifies variation and applies changes in the 5Ms to optimise production. The system includes an NPM-GP/L screen printing machine, which can automatically implement production line changes; the Auto Setting Feeder, an automated component supply system; and the NPM-GH modular mounter, which boasts industry-leading mounting accuracy. This new intelligent cyber-physical system brings these technologies together and enables autonomous control of 5M production process variables, resulting in optimal production.
The same approach can be seen in our Robot and Welding solutions. The integrated Welding Management System, called iWNB, delivers stable production and productivity improvements through the digitalisation and virtualisation of equipment operational status and quality information. As a result, the system helps the shop floor by eliminating failures and avoiding equipment failures. It also meets management needs by reducing production costs, saving on labour requirements and improving productivity.
Of course, manufacturers come in all shapes and sizes and the larger systems can be heavy initial investments for the ultimately large TCO returns. With this in mind, we have also introduced the modular PanaCIM Manufacturing Execution System as a software solution for any size manufacturer and mid-range production systems.
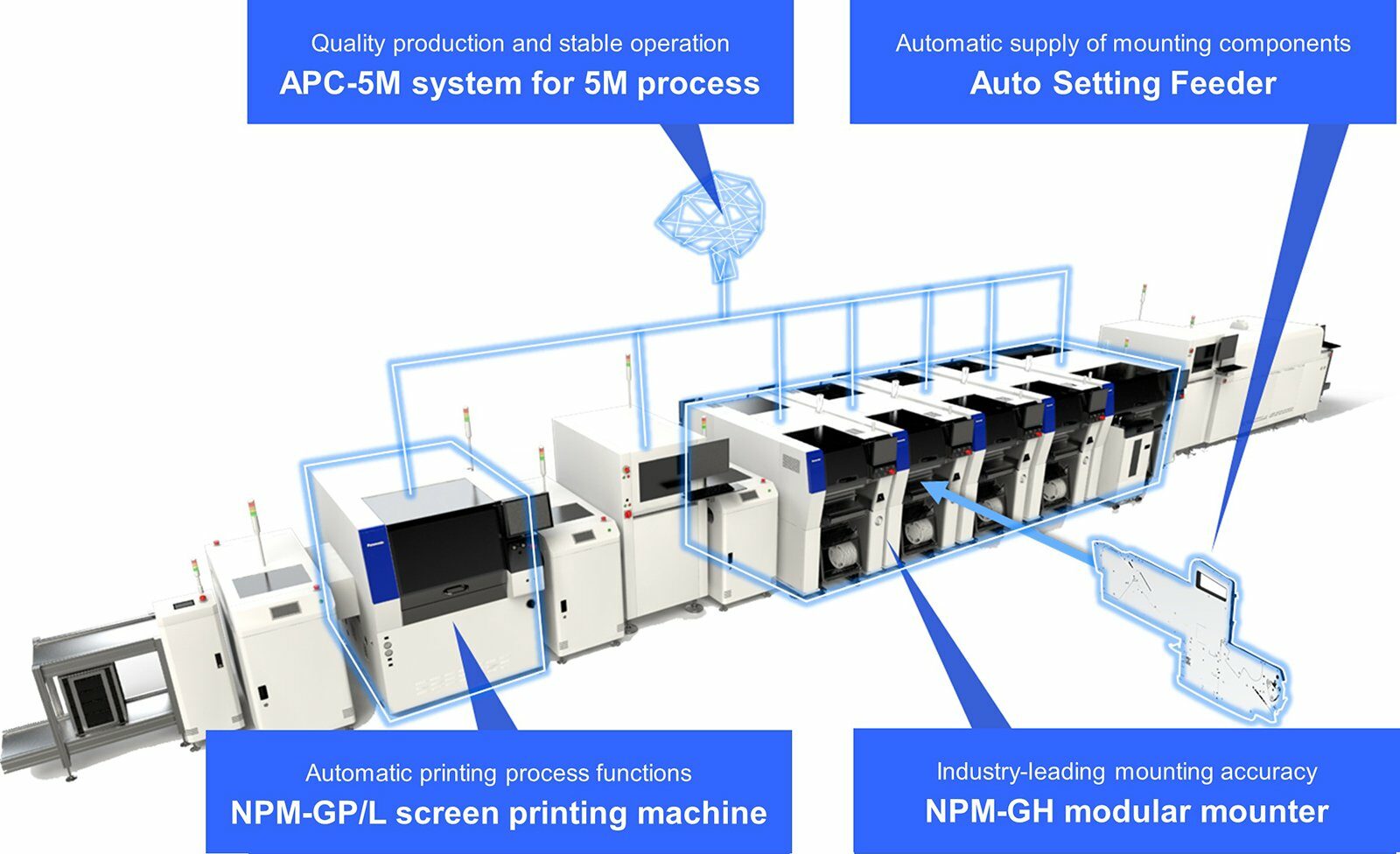
Meeting the evolving need
Of course, to continue to meet the evolving needs of European manufacturers, we must also continue to develop our own capabilities. That is why we are investing in customer-facing personnel to listen closely to the needs of our customers and help them to assess requirements and find new operational solutions. It’s why we also continue to invest in software engineers and work in close collaboration with partners; all to accelerate connectivity and automation for our customers.
Another recent evolution that will be a real asset to our central and Eastern European manufacturing customers is the establishment of our new service centre in Budapest. It brings us even closer to our customers, enhancing our abilities to meet their business needs.
The move of Panasonic Factory Solutions to become part of Panasonic Connect Europe last year was another important evolution. Now part of the business-to-business organisation, we can share in their “connect” vision and together will be able to offer even further connected benefits and synergies to our manufacturing customers in the future.
So, as you can see, the successful future of European manufacturing revolves around the development of connected smart factories. By bringing together our global production experience, new automated intelligent solutions and continuing to closely listen to the needs of our customers, I believe we are in the best position to deliver on that future.
Take a closer look at how we can help your manufacturing organisation to connect. https://eu.connect.panasonic.com/gb/en/products/smart-factory-smt-tht-fatp-and-beyond
Read more insights…
blog
Navigating Change: How Technology Can Power European Business Transformation
European organisations face a challenging 2025 with an uncertain socio-economic backdrop but there are also incredible opportunities being delivered by the latest technologies, explains Shusuke Aoki, new CEO & Managing Director at Panasonic Connect Europe. Now is the time to be bold and grasp that technological opportunity.
whitepaper
Integrating Generative AI into Sales
Until the public release of ChatGPT in November 2022, the debate about the impact of generative AI on work was largely academic. In the short time since its launch, the discussion has become very real. Generative AI is changing the way people work – and fast.
blog
The Future of B2B Marketing Requires a New Marketer
The last industrial revolution changed the way we work forever. The next one is happening right now. But this time, it’s not about steam engines or assembly lines. It’s about artificial intelligence (AI) and its power to reshape B2B marketing as we know it.
whitepaper
Expert Roundtables: Automation & AI in Electronics Manufacturing
In this research we explore the appetite for different wireless technology adoption, expected applications and benefits, the maturity of rollout projects, any barriers to adoption and general viewpoints about each technology.
Sorry there was an error...
The files you selected could not be downloaded as they do not exist.
You selected items.
Continue to select additional items or download selected items together as a zip file.
You selected 1 item.
Continue to select additional items or download the selected item directly.
Share page
Share this link via:
Twitter
LinkedIn
Xing
Facebook
Or copy link: