Kruimelpad
Panasonic Factory Solutions Europe
Your partner for production equipment and automated manufacturing solutions.
Who we are
Smart Factory Solutions for any mix, any volume
Panasonic belongs to the global leading companies in the sector of the Smart Factory. Our unique DNA being a manufacturer and a total solutions provider enables us to understand the needs of our customers and to provide them with tailormade solutions for today’s challenges to be prepared for the industry of tomorrow.
Our dynamic and powerful software, managing our high-end equipment including 3rd party machines, provides our customers with a connected and responsive production environment. Any mix, any volume any time flexible to your needs with full process optimization.
Based on over 100 years of manufacturing and engineering experience, Panasonic offers trusted technology and innovation as your best partner in a connected future.
Connect to the Factory of Tomorrow
Our Solutions. Your Smart Factory
World-leading Panasonic technology matching your manufacturing needs with over 100 years of engineering experience and a wide range of factory solutions including SMT, THT, Robot & Welding, Microelectronics, UA3P equipment, and more.
Best-in-class Panasonic Software created in-house as a tailor-made dynamic solution to your manufacturing challenges: production line design, resource planning, traceability and continuous process optimization for a fully connected factory.
Trusted Panasonic Service with a strong network and trainings facilities all over the world. Providing support, machine & software trainings.
Our Divisions. For your Manufacturing
Panasonic Factory Solutions Europe, headquartered in Ottobrunn, near Munich, provides industrial products, solutions and services in Europe. The company’s portfolio covers production equipment for the electronic industry, software solutions, welding robots and automated manufacturing solutions across a broad range of industries.
Panasonic Factory Solutions Europe consists of the following business units:
- Electronics Manufacturing Solutions (Pick & Place equipment, printers and laser markers for SMT and THT manufacturing)
- Microelectronics (Plasma cleaning, dry-etching and plasma dicing, flip-chip bonding)
- Robot & Welding Systems (Welding and Handling Robots, turn-key PerformArc Cells, Laser Welding systems)
- Solution Engineering (Software Solutions like PanaCIM and ProcessTracker for smart manufacturing and digitalization for Industry 4.0)
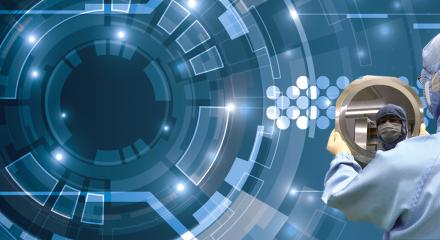
Microelectronics Solutions
With decades of experience we are continually improving our technologies.
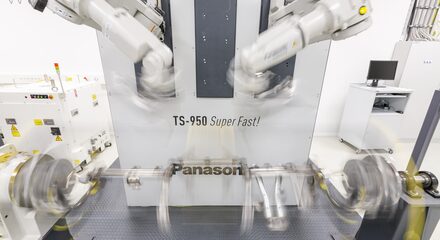
Robot & Welding System Solutions
For more than 60 years, Panasonic is developing welding technology products.
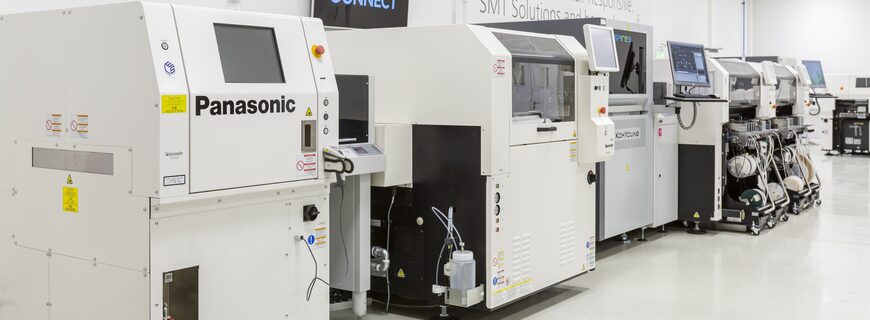
Smart Manufacturing
In the SMT area we offer turnkey solutions for your manufacturing challenges from our portfolio of best-in-class hardware and software products for overall optimization.
"Manufacturing is at the heart of what we do. And our collective knowledge and first-hand experience makes us the industry-leading solutions provider our customers know. "
Head of Factory Solutions Europe
Product Line Up SMT, THT, FATP and beyond
Printing (SMT)
SPV
The SPV Stencil Printer offers a variety of options to suit different PCBs and production processes for consistent high quality. With its high 10s/PCB cycle time, the SPV eliminates bottlenecks and ensures quality by self-cleaning after every PCB. Three conveyors and the PCB identification function provide different automatic printing set ups for a high throughput. With the machine-to-machine-communication option the SPV Screen Printer is using APC correction data to correct positional printing errors. The SPV Stencil Printer can print multiple 350x300mm (M-size) boards simultaneously. This lowers WIP inventory and reduces changeover times by processing up to 4 unique products at once. The configuration minimizes capital expenditure by reducing printer investment by 50% and maximize the floor space utilization with new hybrid board handling concept and the multi-stage board handling conveyors.
Printing (SMT)
SPV-DC
The Stencil Printer SPV-DC enables high efficiency dual lane production in a compact design. The printer is designed for high speed production without changeovers. To reduce running costs the SPV-DC is equipped with the award-winning paperless cleaning function. Solder paste can refill automatically. Solder mask and the final printing result can be verified with an internal inspection. With the machine-to-machine-communication option the SPV-DC is using correction data to correct positional printing errors. The high-speed printer SPV-DC can print on board sizes from 50 x 50mm to 350 x 300mm. With the dual lanes the printer provides a cycle time of 13s, including transfer, positioning, recognition, high-precision printing and respective cleaning. Due to the non-stop changeover, the SPV-DC allows you to prepare the next production while running the printing process.
Printing (SMT)
NPM-GP/L
The fully automated printing solution is part of the "Autonomous Factory" Concept - a factory that immediately responds to every situation and continues to evolve autonomously. Ensuring the production of non-defective items through the integrated control of autonomous uninterrupted mounting lines and floors independent of any human intervention and judgment.
Placement (SMT)
NPM-VF
The NPM-VF is equipped with a double portal. The SMD and THT components are placed by one placement head per portal. A wide variety of vacuum pipettes and grippers are available. The pick and place machine can be used in single or dual lane mode. The NPM-VF reaches a speed of up to 4,500cph and can process component sizes from 5x5mm up to 130x35mm and 60mm height. Active cutting and clinching tools are integrated which detach THT components from the radial and axial feeders. Clinching directions as well as pin lengths per THT component can be defined via the assembly program. Beside the radial and axial feeders, the NPM-VF can be equipped with all common standard feeder systems for SMD components. The flexible NPM-VF is an ideal machine for cycle-optimized production, especially for companies that must process both types of components due to the increased demand from power electronics for THT assemblies. This efficient pick and place machine contributes to reduce manpower requirements and to consistent production with high productivity, flexibility and high-quality pick and place results.
Showing 4 of 20
Product Line Up Robot & Welding
TAWERS Arc welding system solution
TAWERS WG3 Arc welding system
Optimum welding processes are achieved by utilising an integrated inverter power source within the robot controller, ensuring complete synergy within the common control system. This ensures that the established benefits and advantages of the existing TAWERS Fusion Technology are also now available for use for the range of MIG, MAG and DC TIG welding process.
TAWERS Arc welding system solution
TAWERS WGH3 Arc welding system
Optimum welding processes are achieved by utilising an integrated inverter power source within the robot controller, ensuring complete synergy within the common control system.This ensures that the established benefits and advantages of the existing TAWERS Fusion Technology are also now available for use with WGH3.
TAWERS Arc welding system solution
TAWERS WG4 Arc welding system
TAWERS WG4 Arc welding system
Industrial robots
TS series
External cable management systemExternal torch cable and wire (+) Big and therefore good wire curvature (-) Large interior due to cable weight and movement Through-arm cable management systemTorch cable and wire through the hollow shaft (+) Small interior due to outside lying cables (-) Problematic wire management
Showing 4 of 11
Product Line Up Microelectronics
Microelectronics
APX300 Dry Etcher
The APX300 (option S) Dry Etcher is the perfect dry etching equipment for silicon and compound semiconductors. It incorporates a multi-wafer direct cooling system for optimal control of wafer temperature, as well as MSC-ICP (Multi-Spiral Coil type ICP) and BM-ICP (Beamed-type ICP) plasma sources to generate high density plasma. In this way, it achieves a uniform etching profile in a very short timeframe. Building upon the single wafer process chamber of the previous model (Panasonic E620), combined with enhanced process options and two different handling systems, the APX300 (option S) is extremely fast and covers a wide range of process demands.
Features and benefits of Panasonic's APX300 (option S) Dry Etcher The Panasonic APX300 (option S) Dry Etcher can process wafers such as power devices, SAW filters, communication devices, MEMS sensors and many more. The APX300 (option S) is the successor to the previous best-selling Panasonic E620 and utilizes the same single wafer process chamber. Two plasma sources are available: MSC-ICP (Multi-Spiral Coil type ICP) and BM-ICP (Beamed-type ICP). MSC-ICP is Panasonic's latest technology, developed to realize highly accurate processing. BM-ICP offers higher electron density and achieves faster processing, covering a wide range of process demands. In addition, two types of handling systems are available: Atmospheric Loading Supply and Vacuum Load Lock Supply. The Panasonic APX300 (option S) Dry Etcher is CE certified.
Microelectronics
APX300 Plasma Dicer
Plasma dicing is becoming increasingly attractive in the semiconductor market. Dies are becoming smaller and thinner and manufacturers are facing difficulties such as increasing material loss due to the width of the dicing line, mechanical damage to the dies from chipping and increasingly longer processing times due to line-by-line mechanical dicing. Panasonic’s APX300 Plasma Dicer solves these challenges and simultaneously provides a higher quality product with a lower cost of production. Features and benefits of Panasonic's APX300 Plasma DicerPlasma dicing requires a dicing street mask. After the mask is applied to the surface of the wafer and the dicing streets are exposed, the plasma process etches the exposed streets by a chemical reaction. By using a chemical etching process, a chipping-free and particle-free process is achieved. Thanks to the use of mask patterning, narrower street widths are possible – allowing more chips to be designed onto the wafer. Furthermore, the mask patterning allows complete flexibility in chip size, shape and position. The benefits of the Panasonic APX300 Plasma Dicer are: Particle-free and damage-free processHigher chip strengthYield improvementsThe Panasonic APX300 is available in a stand-alone single chamber (1 chamber) or a multi chamber (1, 2, or 3 chambers) configuration. Panasonic can provide a plasma dicing total solution to achieve a damage-free, particle-free, higher throughput and lower overall cost of production. The Panasonic APX300 is CE certified.
Microelectronics
MD-P200 Die Bonder
Unit Level Manufacturing by the synchro-motion of dispensing and bondingThe MD-P200's die bonding is carried out immediately after epoxy dispensing, thereby making it possible to finish the bonding operation before the epoxy has deteriorated. This realizes stable and high quality bonding at all bond positions on a substrate. In addition, the bonding stage camera enables pre-bonding inspection immediately after epoxy dispensing and post-bonding control immediately after the bonding of a die. This process enables manufacturing with real-time quality inspection.User-friendly operationA large touch panel and interactive software realize an easy and reliable operating environment for all users from beginners to experts.
Microelectronics
MD-P300 Flip-chip Bonder
The MD-P300 Flip-chip Bonder is process-flexible, combining flip-chip and thermosonic bonding in a single, small-footprint solution.The MD-P300 contributes to the cost-effective production (high yield, high throughput) of value-added devices. The MD-P300 can achieve high speed and high accuracy bonding through its low gravity point and lightweight bonding head. The MD-P300 supports 300 mm (12") wafers, and is an ideal solution for COB hybrid assembly in combination with an in-line Panasonic SMT placement machine.The MD-P300 is capable of fast cycle times and a placement accuracy of +/-5 μm at 0.5 seconds per IC (dry run) - with thermosonic processes at 0.65 seconds, including process times.
Showing 4 of 6
Approach to Technology & Innovation
Easy explained: Learn more about our Philosophy and Approach to Technology, Customer Service, and Innovation.
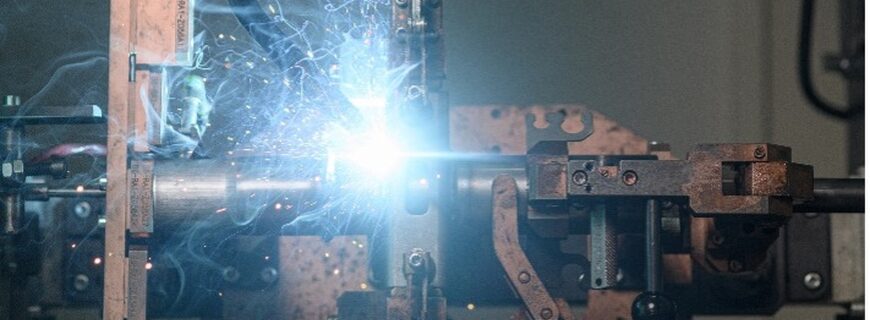
MIG Welding Automation
Precision, Efficiency, and Innovation. Explore Panasonic's MIG welding technology.
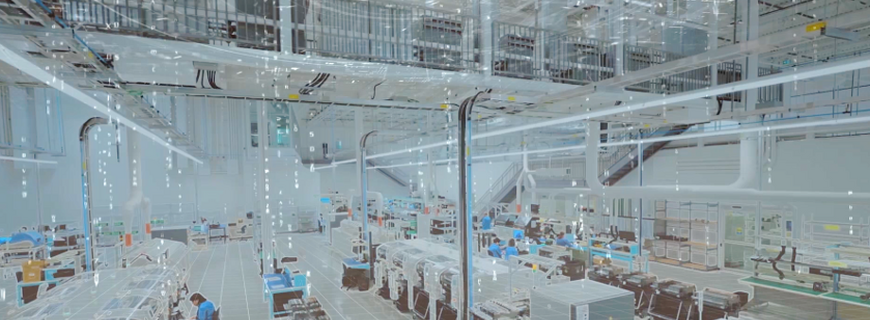
Surface Mount Technology
Precision, Innovation, and Efficiency: Explore Panasonic's Surface Mount Technology
News
Always be up to date with our latest manufacturing blog articles and news.
2025
2025
Event
Schweisstec 2025
Experience the latest robotic welding technology and connect with our experts to discover welding technologies, software applications and service - all from Panasonic.
2025
Case Study
Driving Sustainable Growth: Incap UK Expands SMT Capabilities with Strategic Investment
Incap UK needed to modernise its SMT operations to meet increasing customer requirements across key sectors, including NHS medical devices and defence technology.
Blog
UA3P: Precision That Shapes the Future of Optics
In today's world of ultra-high-definition cameras and cutting-edge optical technology, precision is everything. Whether you're snapping an 8K video with a compact camera or powering advanced automotive systems, the optical components behind the scenes must meet nanometer-level accuracy. But how do you ensure such microscopic perfection? The answer lies in world-class metrology.
Blog
The Keys to Efficient Manufacturing: Smart, Predictive, and Fully Connected
Staying competitive means more than just keeping the production line moving—it requires real-time adaptability, predictive insight, and seamless integration.
2025
2025
Event
Save-the-Date: Productronica 2025!
Save-the-Date: Productronica 2025! Panasonic Factory Solutions Europe invites you to join the interactive event "Autonomous Factory Tech Days" in Munich. Experience our Panasonic Campus Munich, the brand center for Panasonic in Europe, and discover more about the future of manufacturing.
2025
2025
Event
Schweißen & Schneiden 2025
Experience the latest robotic welding technology and connect with our experts to discover welding technologies, software applications and service - all from Panasonic.
2025
Case Study
Caring for Care – with a clever welding production line
The newest production line is supposed to produce four alternatives of the same product with ideally no ramp-up time, perfect welding results and zero tolerance for mistakes.
2025
Case Study
All Connected Seamless by Software: From Production Line to Business Report
Fully integrated production planning and control from machine software to software applications higher up in the automation pyramid.
Blog
No measurement, No production
In the 1980s, Panasonic was the first company in the world to commercialize glass-molded aspheric lenses. "No measurement, No production." This slogan was born during difficult challenges that Panasonic was facing. At this point, the development and production of the UA3P – the Ultrahigh Accurate 3-D Profilometer started and has become a gamechanger within the industry.
Blog
Empowering Success: Panasonic's Dynamic Distribution Partner Network
In today's competitive business landscape, building strong, collaborative relationships is key to driving growth and innovation. Panasonic Factory Solutions Europe has a strong European-wide partner network – a robust and dynamic alliance that drives innovation and excellence across the electronics manufacturing industry.
Blog
Revolutionizing Surface Mount Technology with AI
Surface Mount Technology (SMT) has been a cornerstone in modern electronics manufacturing, enabling the production of high-performance electronic devices. Over the years, several advancements within the SMT industry have significantly enhanced speed as well as accuracy in the assembly process.
Blog
Unmasking the Truth: More Myths in Electronics Manufacturing Busted – Part 2
Part II: Every industry has its share of rumours and myths, and the electronics manufacturing sector is no exception. But how can we separate fact from fiction? Let's debunk some of the most persistent myths in the world of electronics manufacturing and uncover the truth!
Blog
Unmasking the Truth: Debunking the Biggest Myths in Electronics Manufacturing
Within every industry, rumours and myths are a common thing. But how do we know what’s real? Let’s clean up with some of the biggest myths within the electronics manufacturing industry!
2024
Case Study
Paving the way for digitalization of the damper shopfloor
Increasing speed, flexibility and operator-friendliness of a thyssenkrupp Bilstein production line via retrofit upgrade to the new Panasonic TAWERS G4 Welding Robot System.
Article
New Panasonic Auto Setting Feeder Brings Autonomous SMT Production One Step Closer
The Panasonic Auto Setting Feeder is a breakthrough in automated parts supply with automatic loading improving work efficiencies by reducing labour and loss rate while enhancing daily operations on the shop floor.
Blog
Automated Parts Supply: A Revolutionary Supply Technology to Transform Manufacturing
In the fast-paced world of technological innovation, breakthroughs come and go, but every once in a while, a development emerges that has the potential to redefine the industry. Today, we are excited to introduce a revolutionary technology that promises to do just that. This groundbreaking innovation is set to transform material supply in modern production sites. Let’s see what it means for the future of our industry.
2024
Case Study
Auvidea partners with Panasonic to scale its fast-growing AI carrier board business
When Auvidea decided to take its production in-house, Panasonic Connect Europe was on hand to instantly meet its SMT needs and provide critical ongoing support to help the business continue to grow.
Blog
Resilience in electronics manufacturing: Panasonic’s autonomous factory
Many production facilities are still highly dependent on the knowledge and manpower of their employees. This is particularly relevant as the manufacturing industry is currently facing various challenges. These include the shortage of skilled workers as well as complex manual production steps such as splicing, which is used in the production of printed circuit boards (PCBs).
Blog
Visionary Insights: Exploring the Impact of Computer Vision in Electronics Manufacturing
The manufacturing sector has the highest expectations of productivity increases generated by Computer Vision technology, indicating the wide range of applications it has in this sector. From operational use in automated precision pattern cutting and welding, to adjacent processes such as quality control, inspection, monitoring, and packaging, Computer Vision can accelerate production without compromising quality.
Blog
Innovating Assembly Processes for Odd-Shaped Manufacturing
Thinking about manufacturing, we often think of big production facilities with fully automated production and assembly lines. This could be the case for many regular shaped components to be placed on Printed Circuit Boards (PCBs). Looking towards the reality, many electronics products and boards are equipped with odd-shaped components that are even often still placed manually.
Blog
Driving Manufacturing Excellence: Panasonic's Smart Factory Solutions Demo and Training Center
Panasonic Campus Munich emerges as a hub of innovation and technological prowess. Having spent two years as a Software Project Engineer at this dynamic campus, I share my perspective on the exciting world of smart factory solutions, specifically about our SMT demo and training center in Munich.
Blog
The Future of Manufacturing: Steps towards the Autonomous Factory
Ivan Rodrigo Flor Cantos, Factory Solutions Marketing Manager, at Panasonic Connect Europe, tells us more about the Autonomous Manufacturing streaming event that took place at Productronica 2023 in Munich.
Blog
Autonomous manufacturing and supply chain: The cyber-physical automation pyramid
Panasonic is one of the few suppliers offering the complete portfolio of the cyber-physical automation pyramid. It ranges from sensors in the field to AI-driven decisions on the ERP level - but also everything vertically and horizontally from goods inbound solutions over any kind of manufacturing such as SMT, THT, and Final Assembly in electronics manufacturing to efficient intralogistics workflow optimization & traceability to outbound solutions.
Article
Next Generation Robot & Welding G4 Controller Showcased At Schweißen & Schneiden 2023
Panasonic Factory Solutions Europe today introduced its next generation G4 Robot Controller designed to set new standards in Robot Welding for speed, quality, safety and connectivity.
Blog
From Ancient Artistry to Technological Mastery
The evolution of the latest generation of robot welding systems draws on a long history in Japan of incredible innovators renowned for their attention to detail, precision and quality.
Blog
Just weld it: Pioneer and Reliable Partner in Laser and Arc-Welding
Panasonic was founded in 1918 in Japan by Konosuke Matsushita. Since then, Panasonic has constantly developed new technologies and continued to grow its business. In 1957, the Robot & Welding sector was founded with the first arc welding machine.. However, did you know…?
Blog
Closing the automation gap in manual assembly manufacturing
Many people unfamiliar to the world of electronics manufacturing are often surprised by the number of manual assembly processes that are still involved. The challenge of placing larger or odd-shaped components on a Printed Circuit Board (PCB) still requires human assistance.
Stay connected!
Enjoy all the very latest news and views from Smart Factory Solutions delivered direct to you. If you want to stay in touch with the news from Panasonic, now’s your chance. You can register to join the community – your source of all things. We are here to help! Contact us if you have an inquiry or question.
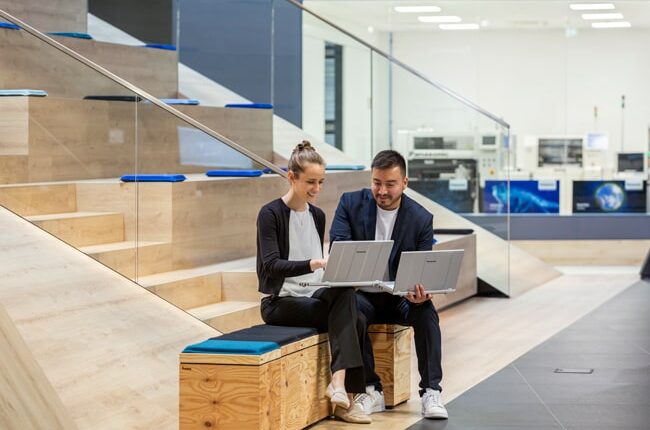
Thank you, we've received your submission, and we'll be in touch soon!
Pagina delen
Share this link via:
Twitter
LinkedIn
Xing
Facebook
Or copy link: