Breadcrumb
Robot and welding systems help to join the dots to autonomous manufacturing
Written by Peer Schumacher
Head of Electronics Manufacturing Solutions
"A shortage of skilled welding labour and a desire for European manufacturers to localise their supply chains back on the continent is accelerating the move towards robot and welding systems and ultimately autonomous manufacturing."
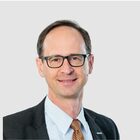
Head of Electronics Manufacturing Solutions
To the untrained eye, there was always something fascinating about the job of a welder. The huge protective helmet covering the eyes and facial expressions of the person inside. The sparks that fly as they solder in industrial surroundings. But this image is one that is rapidly fading as a series of global and commercial pressures converge.
Manufacturers that require welding – from vehicles, ships and their components, to wind turbines – are facing a shortage of skilled labour. In Europe, welders have already been identified by the EU as a skills shortage and the US is predicting they will have 400,000 less welders than needed by 2024. Those welders that remain are in high demand and costs are spiralling. Combine this with the trend for European manufacturers to localise their supply chains and bring production back to the continent and there are challenges brewing. This is only possible if they continue the move towards ever more automation and industry 4.0. When you consider all these factors, the reasons for the rise in interest and increasing deployment of robot and welding solutions becomes clear.
Complete solution range
A major player in robot and welding systems in Asia with more than 60 years’ experience, it’s no surprise that Panasonic is also increasingly in demand across Europe with manufacturers facing these increasing commercial pressures. The company has automated welding solutions for all processes, such as aluminium, stainless steel and steel. It has also developed a unique integrated robot and welding solution called TAWERS, which combines the robot and controller with the welding power source and servo wire feeder into a single unit.
Alongside this, it offers its Laser Processing Robot Integrated System Solution (LAPRISS). The system uses Panasonic’s direct diode laser, which is applicable to metal cutting and welding, as well as the rapidly growing next generation thermal processing fields such as 3D printing, surface processing, and multi material processing for (non) ferrous metals.
Panasonic’s patented Wavelength Beam Combining (WBC) technology produces direct diode lasers with high power and a superior beam quality. The laser has unmatched performance in welding and cutting. It also simplifies manufacturing processes by delivering wider process windows, minimising weld spatter, and increasing processing speeds.
Management for automation
As well as the robot and welding systems themselves, Panasonic also offers a wide range of automation tools to embed the systems into an automated operation. For example, the visual weld inspection solution called Bead Eye removes the need to carry out inspections manually. Bead Eye can carry out comparative inspections using non-defective weld data as a master reference. It can also use its AI engine, based on Panasonic’s own extensive welding experience in its own operations, to identify faults such as pitting.
But to automate beyond the production line, Panasonic has also developed its own weld management system called iWNB (integrated Welding Network Box) to correct, record and analyse facility data automatically to solve production issues around welding processes to improve productivity, quality and traceability.
Lastly, with welding skills in short supply, Panasonic has simplified teaching with its Virtual Robotic Programming System (VRPS). The solution uses VR equipment to simplify robot teaching with intuitive operation using actual workpieces – radically simplifying and reducing programming time.
These robot and welding systems, with automated defect detection, management to improve productivity and traceability and the use of virtual reality technology to simplify and speed up programming are all essential building blocks for the ultimate ambition of autonomous manufacturing. The different elements can be introduced gradually to meet the demands and requirements of each individual manufacturer but ultimately they have been built to work seamlessly together to help deliver the Industry 4.0 vision that manufacturers aspire to.
Read more insights…
blog
Fighting Food Waste with AI and Digital Innovation
Fresh food is the lifeblood of grocery retail. It draws in customers, sets a store apart, and drives daily foot traffic. But this advantage comes at a cost. The perishable nature of fresh products means that ensuring on-shelf availability often leads to overstocking—and with it, high levels of food waste and lost margin.
article
PANASONIC AUTOMATES HAELVOET PRODUCTION LINE WITH G4 WELDING SYSTEM
Panasonic’s TAWERS G4 Welding Robot System provides the desired production flexibility and accuracy for leading medical furniture provider, Haelvoet.
blog
The Keys to Efficient Manufacturing: Smart, Predictive, and Fully Connected
Staying competitive means more than just keeping the production line moving—it requires real-time adaptability, predictive insight, and seamless integration.
article
PANASONIC SOFTWARE INTEGRATES SHOPFLOOR & WAREHOUSE FOR KEMPTRON OY
Panasonic’s software solution integrates Kemptron’s production line with third-party warehouse management systems, increasing efficiency and autonomy for the Finnish electronics manufacturer.
Sorry there was an error...
The files you selected could not be downloaded as they do not exist.
You selected items.
Continue to select additional items or download selected items together as a zip file.
You selected 1 item.
Continue to select additional items or download the selected item directly.
Share page
Share this link via:
Twitter
LinkedIn
Xing
Facebook
Or copy link: