Paving the way for digitalization of the damper shopfloor
Breadcrumb
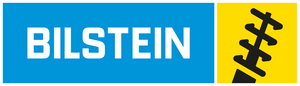
Paving the way for digitalization of the damper shopfloor
Increasing speed, flexibility and operator-friendliness of a thyssenkrupp Bilstein production line via retrofit upgrade to the new Panasonic TAWERS G4 Welding Robot System.
Client: thyssenkrupp Bilstein
Location: Sibiu, Romania
Product(s) supplied: TAWERS WG4 Arc welding system
Challenge
After more than a decade of reliable operations, two welding robot cells were about to face end-of-life. ThyssenKrupp’s team on site, with the support of Panasonic and its partner, was charged with the task to develop a retrofit concept for the automotive welding robot cells in a financially competitive scenario.
Solution
The first welding robot cell has been upgraded to the G4 Welding Robot System– and the de-installed components will function as a source for spare parts for the second oldest robot cell. The upgrade becomes even more efficient with the DTPS offline programming software installed two years ago and a coming iWNB installation, enabling remote digital access to real time production and system operating data.
"To keep the line running, fast reaction times are everything. Sometimes we need instant access to a capable consultant, sometimes spare parts as soon as possible, sometimes a maintenance team available on site in an instance. Panasonic has shown to be fully committed to our support."
Welding Manufacturing Engineer
thyssenkrupp Bilstein Sibiu
The leading automotive supplier maintains 3 plants in Transylvania, the central region in Romania. Near the city Sibiu, more than 1290 employees manufacture OEM damper assemblies, damper assemblies for the aftermarket sector and damper components. The company is one of the biggest employers in the wider region and keen to defend that position. Digitalization plays an integral part in staying ahead of the competition and in achieving the plants’ goals. The increased speed, flexibility and usability of the TAWERS G4, the newest robot system from Panasonic, will become an integral part of the strategy.
In total 6 TAWERS equipped robot welding cells from Panasonic are operating in the plant manufacturing for the aftermarket sector. With the first one installed in 2013 and the latest in 2023. The first ever installed cell has now been upgraded to TAWERS G4.
Reliability – also when it comes to supporting change
Madalin Cirjan is welding manufacturing engineer in Sibiu and part of the team responsible for the process optimization. “Panasonic helped us to find an intelligent and cost-efficient way of retrofitting”, he states. The scope of the first step is replacing the oldest cell, the second oldest is about to be included in an upgrade very soon – but until then, we will utilize parts from cell one as spare parts and therefore increasing the lifespan of cell two and save costs.
Panasonic has always been a reliable partner for thyssenkrupp Bilstein – from planning to installation and after-sales support. In cooperation with SC TOTAL TEHNIQUES SOLUTIONS SRL, a local partner of Panasonic Robot & Welding.
Next to the clever reuse, the new system provides a lot of advantages. The controller processing speed has increased and the communication between controller and robot has been optimised. Additional features like the new generation of teach pendant with touch screen function has also turned out to be very useful.
"It’s the small things, such as during “teach in” programming in the production line, e.g giving programs a name or moving them around, that prolong programming times and can be sometimes annoying. With the touch screen function of the new G4 teach pendant all of that is history.”"
Key account manager
Panasonic Connect
The newly integrated transformer also saves space and costs – still providing the same level of reliability when it comes to transforming to three phase AC 200V.
Madalin emphasizes: “The faster processing time and the touchscreen controller are clearly the main advantages from our side. Also, that the system is more compact due to the newly integrated transformer is positive, even though space saving in our plant is not a big issue, it is still not irrelevant.”
Marking a Milestone – on a longer journey
The installation of the G4 robot system is marking an important milestone of thyssenkrupp Bilstein Sibiu digitalization journey in the factory. “But the journey has not started just now – and it is not at an end”, as Florin Dobrita, Head of Manufacturing and Process Planning at the plant, explains. Further plans for improvement are already existing.
Improving the digital impact on the shopfloor already started in 2022: The first step was the change to Panasonic’s DTPS software, installed in 2022. With the offline programming of the welding process, the production itself is not affected. Florin Dobrita stresses the advantages for the factory: “We can reprogram all parts, or just some parts, while the robot is still running. For a new welding, up to 3 days programming is not uncommon – carrying this out outside the shopfloor saves a lot of time.” Evaluation for collisions or implementing a new welding fixture can easily be tested by uploading our CAD data into the digital twin of the cell.
Vincent Lonsdale stresses: “Before you spend one cent on the prototyping process, you can test and simulate whatever modifications you wish to make offline, in a digital environment. All of this is done outside of the shopfloor – no dust, no heat, no noise. Full focus on the new or modified program, welding fixture or process, without shopfloor production distractions.”
Another advantage Christian Kather, the Technical Training Manager from Panasonic Connect, points out, is Panasonic’s capability to align the cells, even though of different robot types, to one standard – which again allows for more flexibility: “The customer asked us to ensure that the copy function of programs is working from each cell. Which can not only save time, but in case the original indicated robot cell is occupied with another project, there are now 5 more that can be used instantly with almost no additional ramp-up efforts.”
Read more insights…
blog
UA3P: Precision That Shapes the Future of Optics
In today's world of ultra-high-definition cameras and cutting-edge optical technology, precision is everything. Whether you're snapping an 8K video with a compact camera or powering advanced automotive systems, the optical components behind the scenes must meet nanometer-level accuracy. But how do you ensure such microscopic perfection? The answer lies in world-class metrology.
Case Study
Driving Sustainable Growth: Incap UK Expands SMT Capabilities with Strategic Investment
Incap UK needed to modernise its SMT operations to meet increasing customer requirements across key sectors, including NHS medical devices and defence technology.
blog
Fighting Food Waste with AI and Digital Innovation
Fresh food is the lifeblood of grocery retail. It draws in customers, sets a store apart, and drives daily foot traffic. But this advantage comes at a cost. The perishable nature of fresh products means that ensuring on-shelf availability often leads to overstocking—and with it, high levels of food waste and lost margin.
article
PANASONIC AUTOMATES HAELVOET PRODUCTION LINE WITH G4 WELDING SYSTEM
Panasonic’s TAWERS G4 Welding Robot System provides the desired production flexibility and accuracy for leading medical furniture provider, Haelvoet.
Sorry there was an error...
The files you selected could not be downloaded as they do not exist.
You selected items.
Continue to select additional items or download selected items together as a zip file.
You selected 1 item.
Continue to select additional items or download the selected item directly.
Share page
Share this link via:
Twitter
LinkedIn
Xing
Facebook
Or copy link: