Breadcrumb
Resilience in electronics manufacturing
Panasonic’s autonomous factory
Many production facilities are still highly dependent on the knowledge and manpower of their employees. This is particularly relevant as the manufacturing industry is currently facing various challenges. These include the shortage of skilled workers as well as complex manual production steps such as splicing, which is used in the production of printed circuit boards (PCBs). Furthermore, the industry faces lack of material supply as well as very strict traceability requirements. Trying to solve these issues, the digital transformation serves as a driving force for innovation in manufacturing, empowering factories to remain adaptable to any situation and stay competitive in the market.
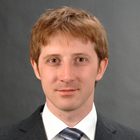
Andreas Prusak
Senior Product Manager
The autonomous factory concept
At this point, Panasonic’s autonomous factory concept comes in where the five pillars of the autonomous factory enable swift responses and autonomous evolution: huMan, Maschine, Material, Method and Measurement (5M). The autonomous factory is based on a convergence of automation and intelligence. It shifts from managing the production manually to automating processes intelligently.
The autonomous factory can be realized through the combination of cutting-edge hardware devices, automation and autonomous production and operation system as well as 5M control and management. Implementing independent optimization of manual executions and decisions enables the establishment of a robust, resilient production while adhering to the production schedule.
Detection of 5M variances
Flexible, efficient, and economical production lines can be set up with the new G-Series platform, which includes the NPM-GP/L stencil printer and the NPM-GH pick and place machine as well as a new Auto Setting Feeder concept, for splice less component feeding throughout the line. Along with the G-series as hardware, goes the APC-5M, Panasonic's APC (Adaptive Process Control) 5M system for 5M process control. It detects and corrects 5M deviations from the optimum and line changes in real time. Within the production environment, the 5Ms detect for variances in operator’s management, machine management, material management, data management as well as measure management. Supported by AI, the APC-5M control system improves and specifies the detection and feedback after each production process - and becomes increasingly precise in the process.
Transformation within all layers of production
The realization of the autonomous factory is based on an overall optimization of the whole production process across all layers of production: from production layer to resource management and management decisions. The aim is to provide a three-layer maximization process through automation and smartification, achieving a factory that autonomously responds to change. The management layer can support maximizing business through efficient investment and high-quality decision making. Looking towards resource management, the maximum resource efficiency should be used in terms of efficient production planning. Lastly, the operating production should operate according to plan without downtime as well as using 5M competency including efficient production equipment.
Have you yet registered for our Connect2Customer Days in October 2024?
Read more insights…
blog
UA3P: Precision That Shapes the Future of Optics
In today's world of ultra-high-definition cameras and cutting-edge optical technology, precision is everything. Whether you're snapping an 8K video with a compact camera or powering advanced automotive systems, the optical components behind the scenes must meet nanometer-level accuracy. But how do you ensure such microscopic perfection? The answer lies in world-class metrology.
Case Study
Driving Sustainable Growth: Incap UK Expands SMT Capabilities with Strategic Investment
Incap UK needed to modernise its SMT operations to meet increasing customer requirements across key sectors, including NHS medical devices and defence technology.
blog
Fighting Food Waste with AI and Digital Innovation
Fresh food is the lifeblood of grocery retail. It draws in customers, sets a store apart, and drives daily foot traffic. But this advantage comes at a cost. The perishable nature of fresh products means that ensuring on-shelf availability often leads to overstocking—and with it, high levels of food waste and lost margin.
article
PANASONIC AUTOMATES HAELVOET PRODUCTION LINE WITH G4 WELDING SYSTEM
Panasonic’s TAWERS G4 Welding Robot System provides the desired production flexibility and accuracy for leading medical furniture provider, Haelvoet.
Sorry there was an error...
The files you selected could not be downloaded as they do not exist.
You selected items.
Continue to select additional items or download selected items together as a zip file.
You selected 1 item.
Continue to select additional items or download the selected item directly.
Share page
Share this link via:
Twitter
LinkedIn
Xing
Facebook
Or copy link: