Breadcrumb
The Material Facts about the Future of Manufacturing
The ability to control and optimise the just in time delivery of materials to the production process is one of the fundamental challenges for the future of automated manufacturing. Peter Barber, Head of Solutions Engineering at Panasonic Factory Solutions Europe, looks at the progress being made.
The production line is set-up and ready to run the next work order. The ERP system says the vital components are in stock but when you look them up in the warehouse - they are nowhere to be found. It’s a mystery to rival a classic episode of the television detective series Columbo! Further investigation finds the reel of components has already been part used on another production line and is waiting to be transferred back to the warehouse. However it is now resolved, it will mean downtime and costly delays. This type of material control issue is one of the fundamental challenges facing manufacturers today.
The headlines are only too clear. Supply chain issues, rising prices and labour shortages are putting the squeeze on manufacturing like never before. To combat these additional costs, manufacturers are accelerating their move to the autonomous factory. The vision is understood. A manufacturing facility that is connected to the supply chain in real-time and able to flex orders and production to meet demand. But where are we today and how close are we to this utopia?
If we take Surface Mount Technology (SMT) production, the process used to create the Printed Circuit Boards (PCB) that go into everything from cars to washing machines and our mobile phones, the production line level control is already well established. The objective is to keep overall equipment effectiveness (OEE) as high as possible. Panasonic offers PanaCIM Basic Modules here for material verification, traceability, production monitoring and production analysis. Production monitoring and analysis are useful additions in that they provide visual alerts to the operators about potential issues that could interrupt production, for example, running low on components. In addition, they keep tabs on the mechanical side of the machine, for example, actively monitoring the feeder to ensure defect rates aren’t rising above target or that predicted maintenance is happening at the correct time.
Production line changeover
The next level is management of the entire SMT production line. Being able to automate and control the changeover of production on an entire line of machines, from different providers. This is where Panasonic Intelligent Line Network Box (iLNB) comes in. Imagine an automotive parts manufacturer making different versions of a unit for many of the big car brands. One day they could be manufacturing units for BMW and the next for Ford. iLNB manages the workflow across all machines in the production line. It ensures the correct programmes are downloaded to each machine, checks Work Order verification and gathers all traceability data into one place – increasing efficiencies and simplifying the process.
Factory floor visibility
At the next level up, things really start to get interesting with factory floor visibility becoming a reality. This where Panasonic’s PanaCIM Advanced module of Material Control operates.
Material Control is the Detective Columbo of the automated manufacturing world. It provides a level of visibility across the entire production process. It’s the glue that makes efficient and automated manufacturing work by understanding how many of each component are available, where they are located, for example in the warehouse or already work in progress (WIP) on another production line, and where and when they need to be moved. Through this unique visibility, the module is able to allocate and plan the delivery of components to pending Work Orders and deliver parts Just In Time and Just In Sequence to the production line for Work Orders that have already started - reducing downtime and increasing productivity.
Entire factory level control
Then we begin to connect in the factory-wide systems with Manufacturing Execution System level software. Panasonic PanaCIM Gen 2 has two modules of interest here. Its Asset Management System can manage, control and optimise the entire production processes across the factory. It provides the ability to automate and control ranges from predicting optimum maintenance times, right down to controlling the optimal performance of different equipment, such as feeders and nozzles, with the ability to interlock these parameters as required.
The second module is Process Tracker, which provides a factory-wide solution for process control and material management. Process Tracker provides total control of the entire manufacturing area ensuring process verification and traceability down to levels such as the amount of torque used on a screw. The potential for this depth of insight and control offers a whole new level of opportunity for fine tuning production, eliminating errors and improving quality and productivity.
Wider supply chain integration
Imagine these systems then connecting into the wider real-time supply chain software applications, powered by AI, that are being driven by Panasonic company Blue Yonder. It’s not hard to then see a world where fully automated manufacturing becomes a real possibility.
But these visions are built one layer at a time. Every manufacturer is starting from a different position. The key to success is increasing visibility, control and automation one step at a time from the individual production machines up to factory wide level.
It will not happen overnight, but Panasonic is putting the building blocks in place to make this vision a reality. Now, in the meantime, where did I put that reel of components?
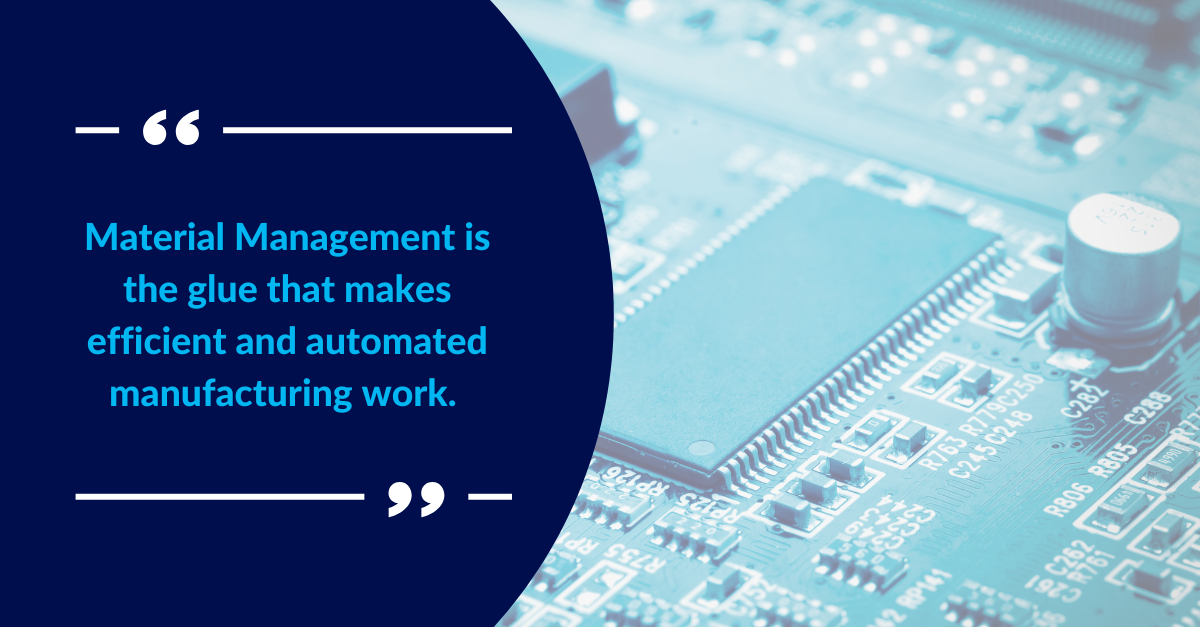
Read the latest news of Smart Factory Solutions.
Read more insights…
article
PANASONIC NEXT LEVEL ROBOT WELDING ON SHOW AT SCHWEIßEN & SCHNEIDEN
New processes and advanced software show why manufacturers are switching to Panasonic’s all-in-one robot welding platform.
Case Study
Driving Sustainable Growth: Incap UK Expands SMT Capabilities with Strategic Investment
Incap UK needed to modernise its SMT operations to meet increasing customer requirements across key sectors, including NHS medical devices and defence technology.
blog
UA3P: Precision That Shapes the Future of Optics
In today's world of ultra-high-definition cameras and cutting-edge optical technology, precision is everything. Whether you're snapping an 8K video with a compact camera or powering advanced automotive systems, the optical components behind the scenes must meet nanometer-level accuracy. But how do you ensure such microscopic perfection? The answer lies in world-class metrology.
blog
Fighting Food Waste with AI and Digital Innovation
Fresh food is the lifeblood of grocery retail. It draws in customers, sets a store apart, and drives daily foot traffic. But this advantage comes at a cost. The perishable nature of fresh products means that ensuring on-shelf availability often leads to overstocking—and with it, high levels of food waste and lost margin.
Sorry there was an error...
The files you selected could not be downloaded as they do not exist.
You selected items.
Continue to select additional items or download selected items together as a zip file.
You selected 1 item.
Continue to select additional items or download the selected item directly.
Share page
Share this link via:
Twitter
LinkedIn
Xing
Facebook
Or copy link: