Breadcrumb
Innovating Assembly Processes for Odd-Shaped Manufacturing
Thinking about manufacturing, we often think of big production facilities with fully automated production and assembly lines. This could be the case for many regular shaped components to be placed on Printed Circuit Boards (PCBs). Looking towards the reality, many electronics products and boards are equipped with odd-shaped components that are even often still placed manually.
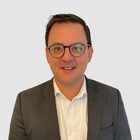
Jérôme Clouet
Senior Product Manager
A technological marvel
As industries worldwide seek to optimize efficiency, reduce costs, and adapt to dynamic market demands, the concept of overall automated manufacturing is nothing new and has emerged as a pivotal strategy. However, but what about automating the placement of odd-shaped components? At this point, our Panasonic NPM-VF machine – a technological marvel revolutionizing smart factory assembly lines – comes in.
The all-rounder pick-and-place machine
NPM-VF is a combined all-rounder pick-and-place machine handling both: SMT and THT components as standard or odd-form components in one placement order. With the NPM-VF, Panasonic has created a platform which makes economical automation in power electronics possible. The technology of the NPM-VF is based on the successful NPM series, and therefore achieves a level of quality in terms of robustness, placement quality and flexibility which has never been achieved before in the industry.
SMD and THT components placement at one time
The odd-form placement machine NPM-VF has been created in accordance with customer requirements. The two portals working in parallel, each with up to three placement heads, provide maximum placement performance with simultaneous flexibility. The SMD and THT components are placed by one placement head per portal. A wide variety of vacuum pipettes and grippers are available. It reaches a speed of up to 4,500cph and can process component sizes from 5x5mm up to 130x35mm and 60mm height.
Active cutting and clinching tools are integrated which detach THT components from the radial and axial feeders. Clinching directions as well as pin lengths per THT component can be defined via the assembly program. Beside the radial and axial feeders, the NPM-VF can be equipped with some standard feeder systems from SMD applications.
Cycle-optimized production
The flexible NPM-VF is an ideal machine for cycle-optimized production, especially for companies that must process both types of components due to the increased demand from power electronics for THT assemblies. Overall, this placement machine contributes to reduce manpower requirements and to consistent production with high productivity, flexibility and high-quality pick and place results.
Interested in learning more? Book your demo with us at our demo center in Munich:
Read more insights…
article
PANASONIC NEXT LEVEL ROBOT WELDING ON SHOW AT SCHWEIßEN & SCHNEIDEN
New processes and advanced software show why manufacturers are switching to Panasonic’s all-in-one robot welding platform.
Case Study
Driving Sustainable Growth: Incap UK Expands SMT Capabilities with Strategic Investment
Incap UK needed to modernise its SMT operations to meet increasing customer requirements across key sectors, including NHS medical devices and defence technology.
blog
UA3P: Precision That Shapes the Future of Optics
In today's world of ultra-high-definition cameras and cutting-edge optical technology, precision is everything. Whether you're snapping an 8K video with a compact camera or powering advanced automotive systems, the optical components behind the scenes must meet nanometer-level accuracy. But how do you ensure such microscopic perfection? The answer lies in world-class metrology.
blog
Fighting Food Waste with AI and Digital Innovation
Fresh food is the lifeblood of grocery retail. It draws in customers, sets a store apart, and drives daily foot traffic. But this advantage comes at a cost. The perishable nature of fresh products means that ensuring on-shelf availability often leads to overstocking—and with it, high levels of food waste and lost margin.
Sorry there was an error...
The files you selected could not be downloaded as they do not exist.
You selected items.
Continue to select additional items or download selected items together as a zip file.
You selected 1 item.
Continue to select additional items or download the selected item directly.
Share page
Share this link via:
Twitter
LinkedIn
Xing
Facebook
Or copy link: