Katoen Natie optimises warehouse management with Toughpad FZ-M1
Breadcrumb
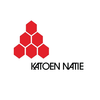
Katoen Natie optimises warehouse management with Toughpad FZ-M1
Success based on user acceptance Katoen Natie is a global player in logistics services. It consists of 400 operational units, with 150 terminals and logistics platforms, employing over 10,000 people and is active in all parts of the world. Each day, over 400 trucks are loaded and unloaded at one of their largest terminals in the port of Antwerp, covering more than 160,000 m² of warehouse space and including nearly 1,000 silos for the storage and transshipment of goods. To ensure these processes run smoothly, Katoen Natie has further developed its existing Warehouse Management System (WMS) on the Toughpad FZ-M1.
Client: Katoen Natie
Location: Antwerp
Katoen Natie is a global player in logistics services. It consists of 400 operational units, with 150 terminals and logistics platforms, employing over 10,000 people and is active in all parts of the world. Each day, over 400 trucks are loaded and unloaded at one of their largest terminals in the port of Antwerp, covering more than 160,000 m2of warehouse space and including nearly 1,000 silos for the storage and transshipment of goods. To ensure these processes run smoothly, Katoen Natie has further developed its existing Warehouse Management System (WMS).
"Given the advances in technology in recent years, we felt there was scope for further optimising our processes and in turn increasing our productivity," explains Jimmy D'Hooge, Scanning & Mobility Project Manager. "What's more, the hardware we were using no longer met the current standards. Our original WMS mostly worked on the basis of paper-based instructions and data input. With the new system, inputting data is a much more straightforward process – as if it were entirely online. By avoiding duplicate entries, we've also been able to reduce the margin of error. Thanks to the touchscreen user interface, it's an intuitive system, so new users can easily be trained."
Katoen Natie designed a completely new user interface within the WMS for processing e-orders. All forklifts in the Warehouse division were fitted with a rugged docking station and tablet.
Trucks in and out within two hours
With over 400 trucks loading and unloading each day, an efficient process is essential. "The length of time a truck stays on site is a very important parameter," explains Kurt Van Roeyen, Operational Manager at Katoen Natie. "So our analysts developed a process whereby each truck is recorded directly in the WMS. The truck driver receives information about where to park their truck, while the forklift operator receives an e-order for loading or unloading the truck. On closing the completed order, the next order is then displayed on their tablet. They then move on to the next location where a truck will be waiting. They enter the license plate of the truck. The WMS confirms whether this is the right truck and specifies where in the warehouse the goods have to be unloaded to. When they have finished, the forklift operator scans the location where the goods have been moved to, and closes the order. All data is automatically forwarded to the WMS. Since we've started using the new system, we've been able to substantially reduce the average time for which a truck remains on site. The risk of incorrect loading operations has also greatly reduced thanks to this system."
Robust hardware for a robust application
After a thorough survey of the hardware market, Katoen Natie opted for the Panasonic Toughpad FZ-M1 7" tablet. "This device is light, boasts an excellent scanner, and has a battery life easily lasting for a full working day. Screen visibility is really good in all conditions, which is important for our forklift operators, who have to keep passing from inside to outside, so the intensity of light on the screen keeps changing.
The tablets are not linked to a specific forklift or operator. If a forklift suddenly breaks down, the operator simply takes the tablet with them to another forklift, so they are able to carry on processing their order."
Integrated docking stations
Katoen Natie uses a docking station specially designed for the FZ-M1, which guarantees the equipment is securely integrated in the vehicles. "This rugged solution is ideal for forklifts, as they don't have suspension like other vehicles, so much higher demands are placed on the shock resistance of the cradle," adds Van Roeyen. "Before we had the current solution, we used to work with a bracket that was too light and a device that was too heavy. So repairs were a weekly occurrence, inevitably leading to a loss of productivity. With the current configuration, we haven't come across this problem yet."
Improved connectivity
Connectivity was a key requirement for Katoen Natie when opting for the Toughpad FZ-M1 tablets. "We get full Wi-Fi coverage in all the outdoor areas between the warehouses, which is where the forklifts close their completed orders and receive new ones. The new orders are downloaded onto the tablet, so operators don't have to be connected to the network to process the order," explains Van Roeyen.
"This means they can carry on working even if they're offline. So operations are not directly affected if there's suddenly no network. As soon as the tablet picks up the Wi-Fi signal again, everything re-synchronizes.” adds D'Hooge.
User acceptance - the key to successful implementation
D'Hooge: “To successfully roll out a new system, it needs to be accepted by the users. For acceptance to be as high as possible, we made sure users were involved in the project at an early stage. They were consulted about the software solutions as well as the choice of hardware. Listening carefully to their feedback was crucial, not only in terms of optimising the application, but also to ensure staff accepted the new way of working."
Future Developments
Katoen Natie is really pleased with the new way of working and intends to roll out the existing platform with the WMS application to other departments. "At the moment, we're trying out the new application in the Silos department: A number of silos have been fitted with an electronic lock controlled by barcodes on the silos. The chance of incorrectly loading goods into the wrong silo is therefore virtually zero," explains D'Hooge. The initial results look great and plans are now under way to roll the solution out to all silos.
Read more insights…
blog
Enhancing the Future of Mobile Fieldwork with AI
As we start to scratch the surface on the business benefits of AI, it’s already clear that this technology will have a profound influence on how mobile field workers operate. So, let’s look at AI’s potential impact over the next 5-10 years.
blog
The Costly Implications of Delaying a Move to Windows 11
With the support for Microsoft’s Windows 10 operating system set to end in October 2025, organisations face an urgent decision – stick with an out-of-date operating system or upgrade to Windows 11.
article
Panasonic TOUGHBOOK Research Highlights Urgency of Windows 11 Migration
Critical infrastructure organisations face increased security, compatibility, performance, cost, and compliance risks if they delay upgrading to Windows 11.
blog
The Digital Battlefield – The Future of Defence Is Happening Now
As warfare evolves with cyber threats, hybrid tactics, and real-time data, Polish defence and tech leaders convened to discuss how digital transformation is no longer optional but essential to operational readiness.
Sorry there was an error...
The files you selected could not be downloaded as they do not exist.
You selected items.
Continue to select additional items or download selected items together as a zip file.
You selected 1 item.
Continue to select additional items or download the selected item directly.
Share page
Share this link via:
Twitter
LinkedIn
Xing
Facebook
Or copy link: