Breadcrumb
Connect2Customer Days:
Showcasing how Customers are benefiting from the Autonomous Factory Concept
Introduced at last year’s Productronica, Panasonic’s own Autonomous Factory Concept has continuously evolved. One year after it’s official market introduction it is now a good time for a reflection – and for collecting feedback from the field as well as for discussions with partners and customers on the future technology roadmap of the concept. We used the Tech Days in October – to do exactly that, together with around 100 customers and partners from all over Europe and for EMS for Automotive as well as general industries alike.
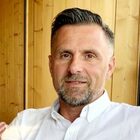
Stefan Hauck
Factory Solutions Marketing Manager
Panasonic Connect Europe
Innovation, collaboration, and cutting-edge technology took center stage at our recent Panasonic Connect2Customer Days, where industry leaders and tech enthusiasts gathered to explore the groundbreaking concept of the autonomous factory. During the tech days, the participants discovered latest technology advancements and had a platform for insightful discussions on the future of automation and smart manufacturing. Let’s recap on the event.
The Autonomous Factory Concept
In today’s fast-evolving electronics landscape, advanced SMT equipment is the gateway to superior performance and competitiveness. State-of-the art solutions are designed for miniaturization and high-density assembly, enabling you to produce complex, multifunctional PCBs with unparalleled precision. The Autonomous Factory Concept is all of that – and combines several suppliers behind the idea helping customers to get more out of their installed base.
The Connect2Customer Days also offered a range of live demonstrations, allowing participants to delve deeper into specific technologies and their applications. These sessions provided valuable opportunities for attendees to engage with Panasonic's latest innovations, ask questions, and gain practical insights into how they can be integrated into their own operations. Partners supporting that were (in alphabetical order): Christian Koenen, Ersa, Griftools, Indium, Koh Young and Nordson.
Revolutionary technology demos such as the world's first auto setting feeder for all tape widths and types, the new G-Series with automated printing process and state-of-the-art process control supported by artificial intelligence (APC-5M) were just a few highlights during the technology days at Panasonic Campus Munich.
Artificial Intelligence, as in every other industry, is gaining foothold in electronics manufacturing as well. Therefore, we have been honored by Panasonic Connect’s head of AI, Margarita Lindahl, hosting a panel discussion with Youjia Feng, also Panasonic Connect, and Solin Ahmad, Koy Young.
From manual to automation, the event explored the transformative journey with a focus on the THT line-upgrade, highlighting the shift from manual processes to advanced automation. Attendees experienced the challenges and solutions for high mix, low volume production as well as discussing prototyping. The event was a hub of ideas and inspiration, featuring exclusive live seminars and demonstrations with guest speakers from our technology partners. A key highlight was the session on smart factory and IoT, showcasing process control supported by AI. The innovation tour offered insights into trends in components, products, and solutions with a guided exploration of the Panasonic Campus in Munich.
Beyond the presentations and workshops, our Connect2Customer Days facilitated networking among industry professionals, fostering an environment of collaboration and knowledge sharing. Attendees had the chance to connect with peers, share experiences, and explore potential partnerships that could drive future innovations in autonomous manufacturing.
As we move forward, the insights and connections gained from the Connect2Customer Days will undoubtedly play a crucial role in shaping the next generation of smart manufacturing solutions. Overall, the event was not just an opportunity to learn about the latest technological advancements, but a chance to be part of the exciting journey towards the autonomous factories of tomorrow.
You missed the Tech Days 2024? We are happy to welcome you in our Smart Factory demo and training center.
Read more insights…
blog
Fighting Food Waste with AI and Digital Innovation
Fresh food is the lifeblood of grocery retail. It draws in customers, sets a store apart, and drives daily foot traffic. But this advantage comes at a cost. The perishable nature of fresh products means that ensuring on-shelf availability often leads to overstocking—and with it, high levels of food waste and lost margin.
article
PANASONIC AUTOMATES HAELVOET PRODUCTION LINE WITH G4 WELDING SYSTEM
Panasonic’s TAWERS G4 Welding Robot System provides the desired production flexibility and accuracy for leading medical furniture provider, Haelvoet.
blog
The Keys to Efficient Manufacturing: Smart, Predictive, and Fully Connected
Staying competitive means more than just keeping the production line moving—it requires real-time adaptability, predictive insight, and seamless integration.
article
PANASONIC SOFTWARE INTEGRATES SHOPFLOOR & WAREHOUSE FOR KEMPTRON OY
Panasonic’s software solution integrates Kemptron’s production line with third-party warehouse management systems, increasing efficiency and autonomy for the Finnish electronics manufacturer.
Sorry there was an error...
The files you selected could not be downloaded as they do not exist.
You selected items.
Continue to select additional items or download selected items together as a zip file.
You selected 1 item.
Continue to select additional items or download the selected item directly.
Share page
Share this link via:
Twitter
LinkedIn
Xing
Facebook
Or copy link: