From Efficiency to Sustainability: Incap’s Strategic Move to Advanced SMT Machinery in the UK
Breadcrumb
From Efficiency to Sustainability: Incap’s Strategic Move to Advanced SMT Machinery in the UK
Challenge
As a contract manufacturer, Incap must address a wide variety of technical aspects to support their customers’ requirements. Their aim is to contribute to reducing the environmental impact and improving their operational efficiency at the same time.
Solution
With the support of new Panasonic manufacturing equipment, Incap is able to achieve several key improvements in terms of energy efficiency, larger production capability, increased operational efficiency as well as transparent material control.
"This investment also improves our SMT operational efficiency, production quality, and site technology. Additionally, it allows for energy savings through real-time intelligent machine monitoring, helping us better serve our current and future customers"
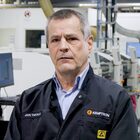
General Manager
Kemptron Oy
Full-service provider
Incap UK is a mid-sized globally operating full-service provider for electronics manufacturing services, serving customers ranging from large multinationals and mid-sized companies to small start-ups in their complete manufacturing value chain. Incap’s factory in UK, based in Newcastle-under-Lyme, provides full turn-key product supply, including PCBAs, electro-mechanical assembly, cable and wire harness assembly, alongside a dedicated standalone rapid prototyping facility, as well as maintenance, repair, and overhaul services. Overall, the factory has 4,400 square metres of total floor space and has experience in manufacturing since 1974, including over 20 years of experience in the security and aerospace markets.
Upgrading for the future
Being a contract manufacturer, Incap must be flexible and offer a variety of technical features to fully support their customers’ requirements and stay competitive in the market. Manufacturing with efficient state-of-the-art production equipment to deliver the best production quality is just one aspect. Profitability, resource efficiency, and energy efficiency are also major factors. Monitoring machines, materials, and production in real-time increases overall operational efficiency and reduces the environmental impact of the company.
In early 2024, Incap upgraded its first production line with two Panasonic AM100 placement machines and the latest fully automated high-precision solder screen printer, the NPM-GPL.
The all-in-one AM100 stands out as a premier solution due to its exceptional reliability, capacity, and flexibility, all while maintaining cost-efficiency. This scalable, high-mix SMT solution is designed to meet the evolving demands of modern production environments. With just one machine, manufacturers can initiate production, and as needs grow, additional units or technologies can be seamlessly integrated.
The NPM-GP/L, part of Panasonic's latest G-Series and autonomous factory concept, exemplifies high-quality printing that adapts to changes in the 5M (man, machine, material, method, and measurement). It boasts a remarkable printing repeatability, ensuring consistent precision. Additionally, it supports automated model changeover to streamline the transition between different production runs and in-time machine monitoring to minimize downtime. The fully automated printing process significantly increases production uptime and ensures the production of non-defective items, thereby maximizing Overall Equipment Effectiveness (OEE).
33% increase in production capacity
The new equipment boosts overall efficiency by approximately 33% through faster machine placement, high-resolution vision recognition systems, and advanced software. This software supports proactive offline setup time reduction, as well as online ready-to-run setup time reduction, optimized feeder exchanges, and live granular production analysis - all including OEE monitoring and reporting.
"Thanks to the investment in the manufacturing equipment, we achieved an initial 33% increase in SMT production capacity for the first line."
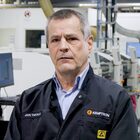
General Manager
Kemptron Oy
Delivering advantages
Additionally, the new production machinery offers energy efficiency, the capability to produce larger PCBs up to 510x460 mm, as well as enhanced screen-printing accuracy, including paste traceability and inspection quality. The increased overall efficiency and optimized material allocation and control, including full traceability of materials and optimized resource and stock allocation, are vital assets for Incap’s modern production environment, aligning with their goals of sustainability, quality, and efficiency.
Trusted partner for the future
While upgrading the first line has already paid off, the second line will be upgraded later this year using identical advanced machinery and software. This strategic update is designed to ensure each stage is optimized before continuing expansions.
The enhancements will enable improved data acquisition capabilities, combining cutting-edge Industry 4.0 architecture for advanced interfacing with future ERP systems. The use of intelligent technologies is instrumental in achieving these improvements and opens new opportunities. Incap’s ongoing collaboration with Panasonic to upgrade technology to new levels of operational excellence reinforces Incap’s strong position in the electronic manufacturing industry.
Read more insights…
blog
Fighting Food Waste with AI and Digital Innovation
Fresh food is the lifeblood of grocery retail. It draws in customers, sets a store apart, and drives daily foot traffic. But this advantage comes at a cost. The perishable nature of fresh products means that ensuring on-shelf availability often leads to overstocking—and with it, high levels of food waste and lost margin.
article
PANASONIC AUTOMATES HAELVOET PRODUCTION LINE WITH G4 WELDING SYSTEM
Panasonic’s TAWERS G4 Welding Robot System provides the desired production flexibility and accuracy for leading medical furniture provider, Haelvoet.
blog
The Keys to Efficient Manufacturing: Smart, Predictive, and Fully Connected
Staying competitive means more than just keeping the production line moving—it requires real-time adaptability, predictive insight, and seamless integration.
article
PANASONIC SOFTWARE INTEGRATES SHOPFLOOR & WAREHOUSE FOR KEMPTRON OY
Panasonic’s software solution integrates Kemptron’s production line with third-party warehouse management systems, increasing efficiency and autonomy for the Finnish electronics manufacturer.
Sorry there was an error...
The files you selected could not be downloaded as they do not exist.
You selected items.
Continue to select additional items or download selected items together as a zip file.
You selected 1 item.
Continue to select additional items or download the selected item directly.
Share page
Share this link via:
Twitter
LinkedIn
Xing
Facebook
Or copy link: