Breadcrumb
Autonomous manufacturing & supply chain
The cyber-physical automation pyramid
Panasonic is one of the few suppliers offering the complete portfolio of the cyber-physical automation pyramid. It ranges from sensors in the field to AI-driven decisions on the ERP level - but also everything vertically and horizontally from goods inbound solutions over any kind of manufacturing such as SMT, THT, and Final Assembly in electronics manufacturing to efficient intralogistics workflow optimization & traceability to outbound solutions.
Written by
Andreas Prusak
Senior Product Manager
Edge devices
Edge devices are used for very dedicated works and processes. Edge Aware Supply Chains feed from real time data at the point of activity to automate actions. The Edge (aka point of activity) is where supply chains create or lose value. Examples could be a shelf in a store or a frozen container in the middle of the ocean. Edge awareness has been traditionally left to human senses, constraining its capacity. Together with Blue Yonder, we are aiming to achieve the autonomous Supply Chain through the combination of Blue Yonder’s software platform and Panasonic Connect’s edge devices and IoT technologies.
Panasonic’s parcel tracking and projection solution Visual Sort Assist (VSA) uses 3D Sensors, generating parcel information all the way. This needs quite a reasonable amount of computing power. Looking at small edge devices like Electronic Shelf Labels (ESL), or Industrial IoT Labels, the aim is to avoid any unnecessary CPU use to save power, so the system battery will last longer. This is an interesting trend in the industry to really power down and send devices to sleep to save power and really work on reducing local power consumption. The real data processing is then put into a scalable Cloud, operating where we have enough resources. Blue Yonder’s Edge Aware Supply Chain Platform converts that data into business information to accelerate decisions.
Smart Factory in a Cyber Physical System
Panasonic’s new 5M conceptual tools will enable customers to drive digital transformation to shape up their production environments for the future. The orchestration of the influences in the production environment by huMans, materials, methods, measurements, and machines (5M) enable efficient digital transformation. Whether this will ultimately be autonomously acting machines, or intelligent systems assisting in decision making is still to be decided.
The first physical production process layer, for example material storage shelfs or the machine line itself, is directly in touch with automation and control systems of the control layer such as the Panasonic Intelligent Line Network Box (iLNB). This manages the workflow, checks work order verification and gathers all traceability data into one place. Another example is Adaptive Process Control (APC-5M), which manages M2M communication in terms of production line feed-forward and feedback communication technology.
At the next level of factory floor visibility and supervisory, the PanaCIM Advanced module of Material Control is the glue that makes efficient and automated manufacturing work. It understands how many of each component are available, where they are located and can allocate and plan the delivery Just in Time and Just in Sequence – all about reducing downtime and increasing productivity.
Within the planning layer, the Manufacturing Operations Optimiser (MFO) creates a digital twin of the production and calculates the required resources. To have minimum stock at production lines we reserve the materials based on work order and can deliver the material not only Just in time to the line but also Just in sequence to the production lines to have minimum changeover time.
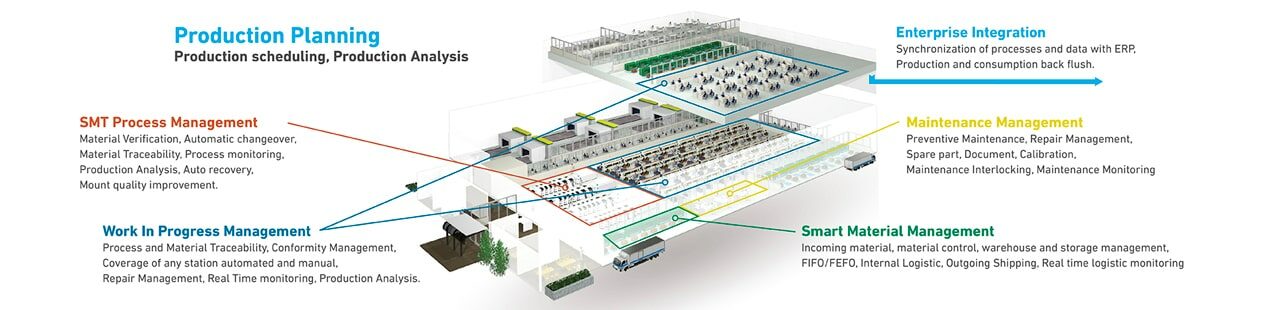
Predictive Maintenance within the Factory
Within the Physical Layer in manufacturing, the entire production process and machines are monitored through enhanced closed loop communication technology, called APC-5M. It detects 5M variations as well as line changes in real-time and ensures a smooth production process without downtime. Thanks to AI, the control system improves and specifies detections and feedback after each production process.
In terms of Industry 4.0, more accurate and meaningful predictions can be made. Big Data automates data collection and analysis, facilitating a better understanding of the status of each system in the production. Based on a customers’ needs and environment, we can support with Real Time Data Processing providing data to a customers’ inhouse data processing tools or offer our Panasonic data analysis and processing tools. Data collected in the physical layer is processed, analyzed and interpreted in the cyber layer.
Regarding the Cyber Layer in manufacturing: Besides good planning and material management, it is essential to understand the status of all the production equipment. With our cloud-based Asset Management we can monitor not only Panasonic equipment but literally every device in the production plant. With Asset Management our customers get the recent condition of the equipment based on the real usage and don´t have to rely on fixed maintenance cycles. Therefore, we can enable very efficient predictive maintenance and perform maintenance before an actual stoppage of production could occur.
To implement predictive maintenance, just in time and just in sequence, we need Real Time Connectivity, master data and an organizational structure. Thanks to real time connectivity to the production, material tracking is possible. Smart Material Management including pick by light and robotic or automated guided vehicle solutions support the automated process. It gives an overview and the possibility to track available materials and their exact location. Master Data includes a production plan with a dedicated number of demanded materials, objectives, machine status and mix as well as desired outcomes. When it comes to organization, it includes operators, discipline, accuracy, knowledge, and know-how as well as logistical structures to implement predictive maintenance.
Benefits of the systems
With VSA, there is an interesting market at the inbound / outbound sorting, of goods. In general, the system delivers up to 40% time savings, a dramatic error reduction and also brings digitalisation benefits into parcel processing. As an example, the system can add further information like volumes and weights to the carrier data.
In terms of ESL, they help deliver 100% error reduction and 80% time savings on price tag updates. In general, we provide a Gemba discussion to our customers. So, we are not there to come with 1 piece of VSA or ESL. We usually check the workflows overall, check if the systems fit the purpose, give KPIs and ROI Predictions, check what workflows might need some additional attention and suport also solutions around the supply chain to create a full solution.
Panasonic’ Manufacturing solutions consist of either automating tasks such as troubleshooting / automating material flow or AI driven decision making. Providing solutions in the control and supervision layer such as e.g., iLNB or ensuring common standard interfaces can communicate with third party interfaces, or collecting and processing data that are then implemented in the cyber-AI layer.
By combining the 5M Management (5MM) with the 5M Process Control (5MPC) in production, we set the foundation for the autonomous factory. 5MM reduces the Total Cost of Ownership (TCO) by managing 5M efficiently with minimal investment and maximising the resource efficiency. Thanks to 5MPC, we have an autonomous control of production conditions and can maximise the output as well as the Overall Equipment Effectiveness (OEE) to ensure the achievement of the production plan. The main pain points such as production down time or limited available labour force are reduced.
Read more insights…
blog
Fighting Food Waste with AI and Digital Innovation
Fresh food is the lifeblood of grocery retail. It draws in customers, sets a store apart, and drives daily foot traffic. But this advantage comes at a cost. The perishable nature of fresh products means that ensuring on-shelf availability often leads to overstocking—and with it, high levels of food waste and lost margin.
article
PANASONIC AUTOMATES HAELVOET PRODUCTION LINE WITH G4 WELDING SYSTEM
Panasonic’s TAWERS G4 Welding Robot System provides the desired production flexibility and accuracy for leading medical furniture provider, Haelvoet.
blog
The Keys to Efficient Manufacturing: Smart, Predictive, and Fully Connected
Staying competitive means more than just keeping the production line moving—it requires real-time adaptability, predictive insight, and seamless integration.
article
PANASONIC SOFTWARE INTEGRATES SHOPFLOOR & WAREHOUSE FOR KEMPTRON OY
Panasonic’s software solution integrates Kemptron’s production line with third-party warehouse management systems, increasing efficiency and autonomy for the Finnish electronics manufacturer.
Sorry there was an error...
The files you selected could not be downloaded as they do not exist.
You selected items.
Continue to select additional items or download selected items together as a zip file.
You selected 1 item.
Continue to select additional items or download the selected item directly.
Share page
Share this link via:
Twitter
LinkedIn
Xing
Facebook
Or copy link: