Alles nahtlos vernetzt per Software: von der Produktionslinie bis zum Geschäftsbericht
Pfadnavigation
Alles nahtlos vernetzt per Software: von der Produktionslinie bis zum Geschäftsbericht
Voll integrierte Produktionsplanung und -steuerung von der Maschinensoftware bis hin zu Softwareanwendungen, die in der Automatisierungspyramide weiter oben stehen. Die Lösung von Panasonic Connect und seinem Partner SMT House erhöht den Automatisierungsgrad – und damit den Wettbewerbsvorteil seines Kunden, eines innovativen Herstellers von Leistungselektronik.
Herausforderung
Das Unternehmen ist spezialisiert auf Dienstleistungen in der Elektronikfertigung, insbesondere für anspruchsvolle Anwendungen in der Leistungselektronik. Dies erfordert von den Maschinen eine hohe Flexibilität, um auch Sonderbauteile zu bewältigen, aber auch eine vollständige Integrierbarkeit in andere Systeme.
Lösung
Hohe Flexibilität und volle Integration verbinden: SMT House installierte eine komplett neue Fertigungslinie mit einem NPM-GP/L-Drucker und drei NPM-W2 Bestückungsautomaten.
"Unsere High Mix Low Volume-Produktion liefert täglich mehr als 30 verschiedene PCBA-Platinen und insgesamt etwa 2000 einzelne PCBA-Platinen. Wir waren auf der Suche nach einer Lösung, die eine hohe Montagegeschwindigkeit, aber auch einen hohen Automatisierungsgrad und sehr schnelle Rüstzeiten bietet. Einer der Gründe für Panasonic waren die Maschinen, ein anderer die Mietlösung von SMT House und schließlich der gute Service vor, während und nach der Installation."
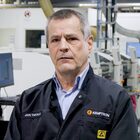
General Manager
Kemptron Oy
Noch ein junges Unternehmen, aber schon eine alte Geschichte: Die Muttergesellschaft Kemppi Group baute einen der ersten Frequenzumrichter auf dem Markt, 1977 den ersten Schweißinverter. Kemptron Oy wurde 2024 als Spin-off der Elektroniksparte von Kemppi gegründet. Die 130 Mitarbeiter mit Sitz in Lahti sind auf Dienstleistungen in der Elektronikfertigung spezialisiert, insbesondere für anspruchsvolle Anwendungen in der Leistungselektronik. Das Portfolio des Unternehmens umfasst mehr als 1.000 verschiedene aktive Leiterplatten. Zu den Fähigkeiten von Kemptron gehört die Herstellung von Leiterplatten, Baugruppen und Transformatoren für industrielle OEM-Kunden, die kundenspezifische Leistungselektroniklösungen benötigen.
Neben der Endmontage der Leiterplatten für die Schweißmaschinen von Kemppi unterstützt Kemptron die andere Schwesterfirma Kempower, die Gleichstrom-Schnellladegeräte für Elektrofahrzeuge, Geländefahrzeuge, Boote oder sogar Flugzeuge herstellt. Durch die Nutzung der Erfahrung und des Know-hows von Kemppi will Kemptron einer der führenden Anbieter von Elektronikfertigung in Finnland werden. General Manager Jari Takala betont: "Strategisch war es sinnvoll, die Elektronikfertigung als eigenes Unternehmen zu trennen, das zwei Schwesterunternehmen, aber auch andere Kunden bedient. Die Kunden in Europa schätzen den Mehrwert und das Prototyping in Finnland mit seiner Erfahrung und seinem Engagement für Service und Qualität."
Flexible und zukunftssichere Hardware
Bisher verwendete Kemptron nur eine Panasonic Through Hole Radial Machine, die SMT-Linien stammten von einem anderen Anbieter. Der finnische Panasonic-Partner SMT House half mit der Idee, die Bestückungsautomaten mit dem europäischen Hauptsitz in München auf die japanische Marke umzustellen. Tatsächlich entwickelte und installierte SMT House eine komplett neue Linie, die einen Drucker, drei NPM-W2-Maschinen, eine SPI- und AOI-Inspektionsmaschine und den Reflow-Ofen umfasste.
Die Anforderungen waren hoch. Jari erklärt: "Die Platzeffizienz muss gut sein und die Maschinen müssen für die Bediener einfach zu programmieren sein." Der Pastendrucker muss sehr robust und qualitativ hochwertig sein. Zusätzlich nützlich ist für den Geschäftsführer der automatische Austausch der Lötpaste, so dass keine Produktionsstopps für die manuelle Zugabe der Lötpaste und kein Risiko besteht, dass die Lötpaste auf der Schablone ausgeht.
Für die NPM-W2 nennt er mehrere Gründe: "Erstens, weil wir in einem High-Mix-Low-Volume-Betrieb arbeiten, müssen wir in der Lage sein, mehr als zehn Rüstumstellungen pro Schicht durchzuführen. Wir brauchten eine Maschine, die damit am besten umgehen kann." Die Montagegeschwindigkeit muss recht hoch sein, und aus dem gleichen Grund musste die Maschine über genügend Feederkapazität verfügen. Darüber hinaus verfügt der NPM-W2 über eine hohe Verfügbarkeit mit nützlichen Features, wie z.B. Frühwarnungen, wenn die Komponenten in den nächsten fünf Minuten zur Neige gehen. Auch die Flexibilität im Umgang mit verschiedenen Bauteilen überzeugte Jari Takala und sein Team: "In der Leistungselektronik kommen sehr viele Prozessoren und Controller zum Einsatz. Alles auf der Platine platziert, doppelseitig, mit beiden Seiten voller SMT-Bauteile."
Abschließend kommt der Geschäftsführer zu dem Schluss, dass die Maschinen zukunftssicher sein mussten, da die Miniaturisierung und Integration verschiedener Funktionen auf derselben Platine im Geschäftsbereich von Kemptron voranschreitet.
Erweiterte Softwareintegration
Die neue Produktionslinie mit Panasonics fortschrittlicher Software PanaCIM konnte nahtlos in das MES, das Epicor Kinetic ERP-System und das automatisierte SMD-Lager integriert werden. "Das System, das wir eingerichtet haben, stellt sicher, dass selbst der "kreativste" Bediener keine falschen Komponenten auf eine Platine setzen kann", sagt Takala.
Vom ersten Tag an war die Ambition des Herstellers klar: Das MES, das mit dem ERP-System verbunden ist, muss sicherstellen, dass die Pick & Place-Maschinen aktualisierte Auftragsinformationen und Materialbedarfe erhalten. "Im Fall von Kemptron synchronisiert es sich mit Bestandsverwaltungssystemen, um die Lagerbestände automatisch auf der Grundlage von Komponenten anzupassen, die bei Pick-and-Place-Operationen verwendet werden", erklärt Matti Luotola, Key Account Manager bei SMT House.
Es gewährleistet die vollständige Wiederholbarkeit bestimmter Prozesse in der Fabrik - eine präzise Kontrolle der Maschineneinstellungen. Es folgen weitere Schritte wie: Überwachung und Nachverfolgung von Änderungen. Schnellerer Produktionsstart und termingerechte Ausführung von Aufträgen.
Read more insights…
blog
UA3P: Precision That Shapes the Future of Optics
In today's world of ultra-high-definition cameras and cutting-edge optical technology, precision is everything. Whether you're snapping an 8K video with a compact camera or powering advanced automotive systems, the optical components behind the scenes must meet nanometer-level accuracy. But how do you ensure such microscopic perfection? The answer lies in world-class metrology.
Case Study
Nachhaltiges Wachstum: Incap UK erweitert SMT-Kapazitäten mit strategischer Investition
Incap UK musste seine SMT-Fertigung modernisieren, um den steigenden Kundenanforderungen in Schlüsselsektoren gerecht zu werden, einschließlich medizinischer Geräte und Verteidigungstechnik des NHS.
blog
Fighting Food Waste with AI and Digital Innovation
Fresh food is the lifeblood of grocery retail. It draws in customers, sets a store apart, and drives daily foot traffic. But this advantage comes at a cost. The perishable nature of fresh products means that ensuring on-shelf availability often leads to overstocking—and with it, high levels of food waste and lost margin.
article
PANASONIC AUTOMATES HAELVOET PRODUCTION LINE WITH G4 WELDING SYSTEM
Panasonic’s TAWERS G4 Welding Robot System provides the desired production flexibility and accuracy for leading medical furniture provider, Haelvoet.
Sorry there was an error...
The files you selected could not be downloaded as they do not exist.
Sie haben Dokument ausgewählt..
Continue to select additional items or download selected items together as a zip file.
Sie haben 1 Dokument ausgewählt.
Wählen Sie weitere Dokumente aus oder laden Sie die aktuelle Auswahl herunter.
Seite teilen
Share this link via:
Twitter
LinkedIn
Xing
Facebook
Or copy link: