Wegbereiter für die Digitalisierung der Stoßdämpferfertigung
Pfadnavigation
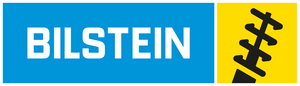
Wegbereiter für die Digitalisierung der Stoßdämpferfertigung
Steigerung der Geschwindigkeit, Flexibilität und Bedienerfreundlichkeit einer Produktionslinie von thyssenkrupp Bilstein durch ein Retrofit-Upgrade auf das neue Panasonic TAWERS G4 Schweißrobotersystem.
Kunde: thyssenkrupp Bilstein
Standort: Sibiu, Rumänien
Product(s) supplied: TAWERS WG4 Arc welding system
Herausforderung
Nach mehr als einem Jahrzehnt zuverlässigen Betriebs standen zwei Schweißroboterzellen kurz vor dem Ende ihrer Lebensdauer. Das Team von ThyssenKrupp vor Ort hatte mit Unterstützung von Panasonic und seinem Partner den Auftrag, ein Retrofit-Konzept für die Schweißroboterzellen im Automobilbau in einem wirtschaftlich wettbewerbsfähigen Szenario zu entwickeln.
Lösung
Die erste Schweißroboterzelle wurde auf das G4 Welding Robot System aufgerüstet – und die deinstallierten Komponenten dienen als Ersatzteilquelle für die zweitälteste Roboterzelle. Das Upgrade wird noch effizienter mit der vor zwei Jahren installierten DTPS-Offline-Programmiersoftware und einer bevorstehenden iWNB-Installation, die den digitalen Fernzugriff auf Produktions- und Betriebsdaten in Echtzeit ermöglicht.
"Um die Linie am Laufen zu halten, sind schnelle Reaktionszeiten alles. Manchmal brauchen wir sofortigen Zugang zu einem kompetenten Berater, manchmal Ersatzteile so schnell wie möglich, manchmal ein Wartungsteam, das sofort vor Ort ist. Panasonic hat gezeigt, dass es sich voll und ganz für unsere Unterstützung einsetzt."
Welding Manufacturing Engineer
thyssenkrupp Bilstein Sibiu
Der führende Automobilzulieferer unterhält 3 Werke in Siebenbürgen, der zentralen Region in Rumänien. In der Nähe der Stadt Sibiu fertigen mehr als 1290 Mitarbeiter OEM-Dämpferbaugruppen, Dämpferbaugruppen für den Aftermarket-Bereich und Dämpferkomponenten. Das Unternehmen ist einer der größten Arbeitgeber in der Region und möchte diese Position verteidigen. Die Digitalisierung spielt eine wesentliche Rolle, um dem Wettbewerb einen Schritt voraus zu sein und die Ziele der Werke zu erreichen. Die erhöhte Geschwindigkeit, Flexibilität und Benutzerfreundlichkeit des TAWERS G4, dem neuesten Robotersystem von Panasonic, wird zu einem integralen Bestandteil der Strategie.
Insgesamt sind 6 mit TAWERS ausgestattete Roboterschweißzellen von Panasonic im Anlagenbau für den Aftermarket-Bereich im Einsatz. Die erste wurde 2013 und die letzte im Jahr 2023 installiert. Die erste jemals installierte Zelle wurde nun auf TAWERS G4 aufgerüstet.
Verlässlichkeit – auch wenn es darum geht, Veränderungen zu unterstützen
Madalin Cirjan ist Ingenieurin für Schweißtechnik in Sibiu und Teil des Teams, das für die Prozessoptimierung verantwortlich ist. "Panasonic hat uns geholfen, einen intelligenten und kosteneffizienten Weg der Nachrüstung zu finden", sagt er. Der erste Schritt umfasst den Austausch der ältesten Zelle, die zweitälteste wird demnächst in ein Upgrade einbezogen – aber bis dahin werden wir Teile aus Zelle eins als Ersatzteile verwenden und so die Lebensdauer von Zelle zwei erhöhen und Kosten sparen.
Panasonic war für thyssenkrupp Bilstein seit jeher ein verlässlicher Partner – von der Planung über die Installation bis hin zum After-Sales-Support. In Zusammenarbeit mit SC TOTAL TEHNIQUES SOLUTIONS SRL, einem lokalen Partner von Panasonic Robot & Welding.
Neben der cleveren Wiederverwendung bietet das neue System viele Vorteile. Die Verarbeitungsgeschwindigkeit der Steuerung hat sich erhöht und die Kommunikation zwischen Steuerung und Roboter wurde optimiert. Auch zusätzliche Features wie die neue Generation des Teach-Pendants mit Touchscreen-Funktion haben sich als sehr nützlich erwiesen.
"Es sind die kleinen Dinge, wie z.B. beim "Teach in"-Programmieren in der Produktionslinie, z.B. Programmen einen Namen zu geben oder sie zu verschieben, die die Programmierzeiten verlängern und manchmal nervig sein können. Mit der Touchscreen-Funktion des neuen G4 teach pendant ist das alles Geschichte.""
Key account manager
Panasonic Connect
Der neu integrierte Transformator spart zudem Platz und Kosten – und bietet bei gleicher Zuverlässigkeit die gleiche Zuverlässigkeit bei der Umrüstung auf dreiphasiges AC 200V.
Madalin betont: "Die schnellere Bearbeitungszeit und der Touchscreen-Controller sind ganz klar die Hauptvorteile von unserer Seite. Positiv ist auch, dass die Anlage durch den neu integrierten Transformator kompakter ist, auch wenn die Platzersparnis in unserer Anlage kein großes Thema ist, aber dennoch nicht irrelevant."
Einen Meilenstein markieren – auf einer längeren Reise
Die Installation des G4-Robotersystems markiert einen wichtigen Meilenstein auf dem Weg der Digitalisierung von thyssenkrupp Bilstein Sibiu in der Fabrik. "Aber die Reise hat noch nicht begonnen – und sie ist noch nicht zu Ende", erklärt Florin Dobrita, Leiter Fertigung und Prozessplanung im Werk. Weitere Pläne zur Verbesserung gibt es bereits.
Die Verbesserung des digitalen Impacts auf dem Shopfloor begann bereits im Jahr 2022: Der erste Schritt war der Wechsel auf die 2022 installierte DTPS-Software von Panasonic. Durch die Offline-Programmierung des Schweißprozesses wird die Produktion selbst nicht beeinträchtigt. Florin Dobrita betont die Vorteile für die Fabrik: "Wir können alle Teile oder nur einige Teile neu programmieren, während der Roboter noch läuft. Bei einer neuen Schweißung sind bis zu 3 Tage Programmierung keine Seltenheit – die Durchführung außerhalb der Werkstatt spart viel Zeit." Die Bewertung auf Kollisionen oder die Implementierung einer neuen Schweißvorrichtung kann einfach getestet werden, indem unsere CAD-Daten in den digitalen Zwilling der Zelle hochgeladen werden.
Vincent Lonsdale betont: "Bevor Sie einen Cent für den Prototyping-Prozess ausgeben, können Sie alle Änderungen, die Sie vornehmen möchten, offline in einer digitalen Umgebung testen und simulieren. All dies geschieht außerhalb der Werkstatt – kein Staub, keine Hitze, kein Lärm. Volle Konzentration auf das neue oder geänderte Programm, die Schweißvorrichtung oder den Prozess, ohne Ablenkungen durch die Produktion in der Fertigung."
Ein weiterer Vorteil, den Christian Kather, Technical Training Manager von Panasonic Connect, hervorhebt, ist die Fähigkeit von Panasonic, die Zellen, auch wenn es sich um unterschiedliche Robotertypen handelt, auf einen Standard auszurichten – was wiederum mehr Flexibilität ermöglicht: "Der Kunde bat uns, sicherzustellen, dass die Kopierfunktion von Programmen von jeder Zelle aus funktioniert. Das kann nicht nur Zeit sparen, sondern für den Fall, dass die ursprünglich angegebene Roboterzelle mit einem anderen Projekt belegt wird, gibt es jetzt 5 weitere, die sofort und fast ohne zusätzlichen Anlaufaufwand eingesetzt werden können."
Read more insights…
blog
UA3P: Precision That Shapes the Future of Optics
In today's world of ultra-high-definition cameras and cutting-edge optical technology, precision is everything. Whether you're snapping an 8K video with a compact camera or powering advanced automotive systems, the optical components behind the scenes must meet nanometer-level accuracy. But how do you ensure such microscopic perfection? The answer lies in world-class metrology.
Case Study
Nachhaltiges Wachstum: Incap UK erweitert SMT-Kapazitäten mit strategischer Investition
Incap UK musste seine SMT-Fertigung modernisieren, um den steigenden Kundenanforderungen in Schlüsselsektoren gerecht zu werden, einschließlich medizinischer Geräte und Verteidigungstechnik des NHS.
blog
Fighting Food Waste with AI and Digital Innovation
Fresh food is the lifeblood of grocery retail. It draws in customers, sets a store apart, and drives daily foot traffic. But this advantage comes at a cost. The perishable nature of fresh products means that ensuring on-shelf availability often leads to overstocking—and with it, high levels of food waste and lost margin.
article
PANASONIC AUTOMATES HAELVOET PRODUCTION LINE WITH G4 WELDING SYSTEM
Panasonic’s TAWERS G4 Welding Robot System provides the desired production flexibility and accuracy for leading medical furniture provider, Haelvoet.
Sorry there was an error...
The files you selected could not be downloaded as they do not exist.
Sie haben Dokument ausgewählt..
Continue to select additional items or download selected items together as a zip file.
Sie haben 1 Dokument ausgewählt.
Wählen Sie weitere Dokumente aus oder laden Sie die aktuelle Auswahl herunter.
Seite teilen
Share this link via:
Twitter
LinkedIn
Xing
Facebook
Or copy link: