Breadcrumb
Unmasking the Truth:
Debunking the Biggest Myths in Electronics Manufacturing
Within every industry, rumours and myths are a common thing. But how do we know what’s real? Let’s clean up with some of the biggest myths within the electronics manufacturing industry!
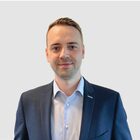
Felix Mögele
Senior Business Development Manager
Production equipment is not flexible, compatible, and modular.
It’s a myth! Because…
… feeders are flexible: Material and feeder preparation on the machine is possible. With the installed Offline Unit Station, even passive feeder preparation is possible. Indeed, with the AM100 it only takes one machine to start off production and extra options can be easily integrated according to requirements.
… feeders have a memory function: Thanks to the memory function, feeders can be taken off and inserted again without manually pairing them again. The machine automatically knows which material is loaded as the component roll is paired with the feeder memory. On our NPM-WX machine, the APC system and automatic recovery are integrated to provide autonomous line control. The incorporated floor-management system and remote-operation option improve utilisation combined with lower labour costs. Feeder set-up and component supply navigation systems are available, helping to reduce the work variations.
… feeders & software can be used with next generations of machines as well: Our latest-generation machines can also operate with older feeders and software since the previous CM line has debuted. This means you can replace only some parts of your SMT machine without changing everything!
Large electronics manufacturing providers see middle size small and medium enterprises (SME) as too small to make business.
It’s a myth!
One of the best examples is the German company Auvidea, a middle size company focusing on the AI sector and NVIDIA Jetson platform. Auvidea already had a small SMT production machine but wanted to look closely at all the major SMT machine manufacturers as a next step and quickly chose Panasonic. “At first, we were worried that Panasonic would view us as too small, but they quickly dispelled that thought,” said Oliver Stelbrink, CTO Auvidea GmbH. “They could see our potential and we could see a path to growing with them.”
The industry is far away from autonomous manufacturing.
It’s a myth!
We are getting their step by step thanks to many technological developments within the last years. As of today, many production sites still rely on their employee’s knowledge and manpower – the so called 5M (Human, Machine, Material, Method, Measurement). The new Panasonic NPM G Series uses Artificial Intelligence (AI) and automated production to improve this 5M process. The entire production process and machines are monitored through feed-forward, feed-backward and closed loop communication technology, called APC-5M. Adaptive Process Control (APC) tracks the correct placement of components based on the solder printing position and transfers feedback to the screen printer in case of misalignment. The latest auto setting feeder technology is also a further step towards autonomous manufacturing: it’s the one of the keys to automation and labor saving as the automatic setting and loading reduces set time drastically, achieves skill-less and splicing-free operations.
For now, we still need human intervention within SMT production, but can already reduce the manpower and simultaneously improve the OEE. And to be continued!
Only large companies with high production volumes and strict regulations need traceability.
It’s a myth!
Traceability itself is important for companies of all sizes as it helps to identify and eliminate the causes of quality problems, which saves costs in the long term and increases customer satisfaction. As an example, our PanaCIM line management software connects digital and physical work, reporting and management areas. From inventory management, maximized factory performance based on a continuous production, total traceability, to real time machine monitoring and optimization and an accurate in-time material supply, PanaCIM allows for more efficient electronics manufacturing. Higher production rates and shorter cycle times can be achieved to make electronics production even more reliable.
Unmasking the Truth: More Myths in Electronics Manufacturing Busted – Part 2
Every industry has its share of rumours and myths, and the electronics manufacturing sector is no exception. But how can we separate fact from fiction? Let's debunk some of the most persistent myths in the world of electronics manufacturing and uncover the truth!
Read more insights…
blog
Fighting Food Waste with AI and Digital Innovation
Fresh food is the lifeblood of grocery retail. It draws in customers, sets a store apart, and drives daily foot traffic. But this advantage comes at a cost. The perishable nature of fresh products means that ensuring on-shelf availability often leads to overstocking—and with it, high levels of food waste and lost margin.
article
PANASONIC AUTOMATES HAELVOET PRODUCTION LINE WITH G4 WELDING SYSTEM
Panasonic’s TAWERS G4 Welding Robot System provides the desired production flexibility and accuracy for leading medical furniture provider, Haelvoet.
blog
The Keys to Efficient Manufacturing: Smart, Predictive, and Fully Connected
Staying competitive means more than just keeping the production line moving—it requires real-time adaptability, predictive insight, and seamless integration.
article
PANASONIC SOFTWARE INTEGRATES SHOPFLOOR & WAREHOUSE FOR KEMPTRON OY
Panasonic’s software solution integrates Kemptron’s production line with third-party warehouse management systems, increasing efficiency and autonomy for the Finnish electronics manufacturer.
Sorry there was an error...
The files you selected could not be downloaded as they do not exist.
You selected items.
Continue to select additional items or download selected items together as a zip file.
You selected 1 item.
Continue to select additional items or download the selected item directly.
Share page
Share this link via:
Twitter
LinkedIn
Xing
Facebook
Or copy link: